Alloying elements on the welding performance of steel
Alloying elements on the welding performance of steel
What are the effects of alloying elements on the welding performance of steel?
For welding wire containing Si, Mn, S, P, Cr, AI, Ti, Mo, V and other alloying elements. What are the effects of these alloying elements on the welding performance, the following are respectively explained:
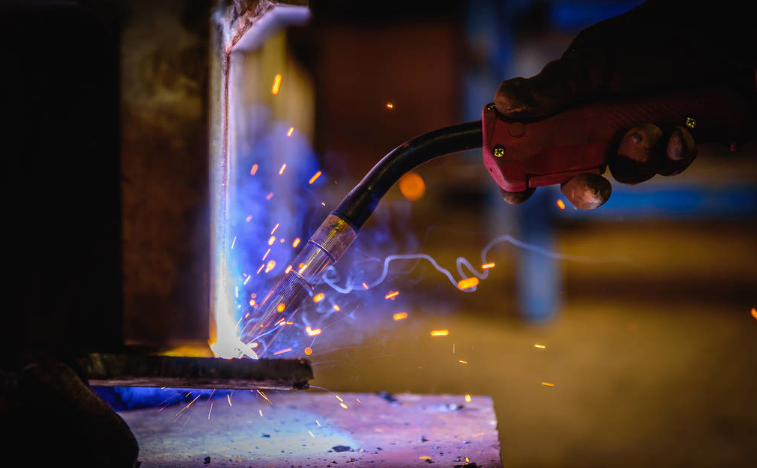
Silicon (Si)
Silicon is the most commonly used deoxidizing element in welding wire. It can prevent iron from combining with oxidation and can reduce FeO in the molten pool. However, using silicon alone to deoxidize, the resulting SiO2 has a high melting point (about 1710°C), and the resulting particles are small, difficult to float out of the molten pool, and easily cause slag inclusion in the weld metal.
Manganese (Mn)
The role of manganese is similar to that of silicon, but its deoxidizing ability is slightly worse than that of silicon. Using manganese alone for deoxidation, the resulting MnO has a higher density (15.11g/cm3) and is not easy to float out of the bath. The manganese contained in the welding wire, in addition to deoxidation, can also combine with sulfide to form manganese sulfide (MnS) and be removed (desulfurized), so it can reduce the tendency of hot cracks caused by sulfur. Since silicon and manganese are used alone for deoxidation, it is difficult to remove deoxidized products. Therefore, at present, silico-manganese combined deoxidation is often used to make the generated SiO2 and MnO composite into silicate (MnO·SiO2). MnO·SiO2 has a low melting point (about 1270°C) and a low density (about 3.6g/cm3). It can condense into a large slag and float out in the molten pool to achieve a good deoxidation effect. Manganese is also an important alloying element in steel and an important hardenability element. It has a great influence on the toughness of the weld metal. When the Mn content is less than 0.05%, the toughness of the weld metal is very high; when the Mn content is more than 3%, it is very brittle; when the Mn content = 0.6 to 1.8%, the weld metal has higher strength And resilience.
Sulfur (S)
Sulfur is often present in steel in the form of iron sulfide, and is distributed in the grain boundary in a network, thus significantly reducing the toughness of steel. The eutectic temperature of iron and iron sulfide is relatively low (985°C). Therefore, during hot working, since the processing start temperature is generally 1150 to 1200°C, the eutectic of iron and iron sulfide has already melted, resulting in cracks during processing. This phenomenon is the so-called "hot brittleness of sulfur". This property of sulfur causes hot cracks in steel during welding. Therefore, the sulfur content in steel is generally strictly controlled. The main difference between ordinary carbon steel, high-quality carbon steel and high-quality high-quality steel is the content of sulfur and phosphorus. As mentioned earlier, manganese has a desulfurization effect. This is because manganese can form high melting point (1600°C) manganese sulfide (MnS) with sulfur, which is distributed in grains in a granular form. During hot working, manganese sulfide has sufficient plasticity, thus eliminating the harmful effects of sulfur. Therefore, maintaining a certain amount of manganese in steel is beneficial.
Phosphorus (P)
Phosphorus can be completely dissolved in ferrite in steel. Its strengthening effect on steel is second only to carbon, which increases the strength and hardness of steel. Phosphorus can improve the corrosion resistance of steel, while plasticity and toughness are significantly reduced. Especially at low temperatures, the effect is more serious, which is called the cold kneeling tendency of phosphorus. Therefore, it is not good for welding and increases the crack sensitivity of steel. As an impurity, the content of phosphorus in steel should also be restricted.
Chromium (Cr)
Chromium can increase the strength and hardness of steel, while plasticity and toughness are not greatly reduced. Chromium has strong corrosion and acid resistance, so austenitic stainless steel generally contains more chromium (more than 13%). Chromium also has strong oxidation resistance and heat resistance. Therefore, chromium is also widely used in heat-resistant steels, such as 12CrMo, 15CrMo, 5CrMo and so on. Steel contains a certain amount of chromium [7]. Chromium is an important element of austenitic steel and a ferritizing element. It can improve oxidation resistance and mechanical properties at high temperatures in alloy steel. In austenitic stainless steel, when the total amount of chromium-nickel is 40% and Cr/Ni = 1, there is a tendency for hot cracking; when Cr/Ni = 2.7, there is no tendency for hot cracking. Therefore, when Cr/Ni = 2.2~2.3 in 18-8 steel, chromium is easy to produce carbides in alloy steel, which makes the heat conduction of alloy steel worse, easily produces chromium oxide, and makes welding difficult.
Aluminum (AI)
Aluminum is one of the strong deoxidizing elements, so using aluminum as a deoxidizer can not only reduce FeO, but also easily reduce FeO, effectively inhibit the chemical reaction of CO gas generated in the molten pool, and improve the ability to resist CO pores. In addition, aluminum can combine with nitriding to fix nitrogen, so it can also reduce nitrogen pores. However, when aluminum is used for deoxidation, the produced AI2O3 has a high melting point (about 2050°C), and it exists in the molten pool in a solid state, which is likely to cause slag inclusion in the weld. At the same time, the aluminum-containing welding wire is prone to splashing, and too high aluminum content will reduce the thermal crack resistance of the weld metal. Therefore, the aluminum content in the welding wire must be strictly controlled and not too much. If the aluminum content in the welding wire is properly controlled, the hardness, yield point, and tensile strength of the weld metal will be slightly improved.
Titanium (Ti)
Titanium is also a strong deoxidizing element, and it can also synthesize TiN with nitriding to fix nitrogen and improve the ability of weld metal to resist nitrogen pores. If the content of Ti and B (boron) in the weld structure is appropriate, the weld structure can be refined.
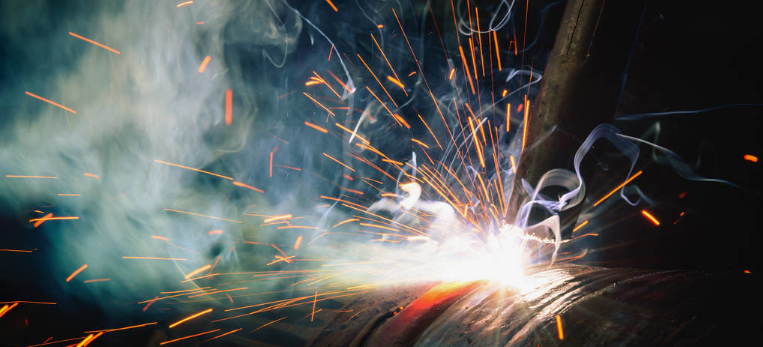
Molybdenum (Mo)
Molybdenum in alloy steel can improve the strength and hardness of steel, refine the grains, prevent temper brittleness and overheating tendency, and improve high temperature strength, creep strength and endurance strength. When the molybdenum content is less than 0.6%, it can improve plasticity. Reduce the tendency of cracks and improve impact toughness. Molybdenum has a tendency to promote graphitization. Therefore, heat-resistant steels containing molybdenum, such as 16Mo, 12CrMo, 15CrMo, etc., contain about 0.5% molybdenum. When the content of molybdenum in alloy steel is between 0.6 and 1.0%, molybdenum will decrease the plasticity and toughness of alloy steel and increase the quenching tendency of alloy steel.
Vanadium (V)
Vanadium can increase the strength of steel, refine grains, reduce the tendency of grain growth, and improve hardenability. Vanadium is a relatively strong carbide forming element, and the carbides formed are stable below 650°C. Time-hardening effect. Vanadium carbides have high temperature stability, which can increase the high temperature hardness of steel. Vanadium can change the distribution of carbides in steel, but vanadium easily generates refractory oxides, which increases the difficulty of gas welding and gas cutting. Generally, when the vanadium content in the weld is about 0.11%, it can play a role in nitrogen fixation, which becomes disadvantageous and advantageous.