Welding of austenitic stainless steel
Welding of austenitic stainless steel
Five major welding problems and treatment measures of austenitic stainless steel
Welding characteristics of austenitic stainless steel: the elasticity, plastic stress and strain during welding are large, but cold cracks rarely occur. There is no quenching hardening zone and coarsening of grains in the welded joint, so the tensile strength of the weld is higher.
The main problem of austenitic stainless steel welding: large welding deformation; due to its grain boundary characteristics and sensitivity to certain trace impurities (S, P), it is easy to produce thermal cracks.
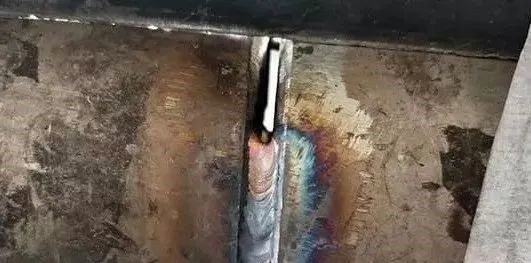
01 The formation of chromium carbide reduces the ability of welded joints to resist intergranular corrosion.
Intergranular corrosion: According to the chromium-depleted theory, chromium carbide is precipitated on the grain boundary when the weld and heat-affected zone are heated to the sensitizing temperature range of 450-850 ℃, resulting in the chromium-deficient grain boundary, which is not enough to resist the degree of corrosion.
(1) For the intergranular corrosion of the weld and the sensitized temperature zone corrosion on the target material, the following measures can be used to limit:
a. Reduce the carbon content of the base metal and the weld, add stabilizing elements Ti, Nb and other elements to the base metal to make it preferentially form MC to avoid the formation of Cr23C6.
b. Make the weld form a two-phase structure of austenite plus a small amount of ferrite. When there is a certain amount of ferrite in the weld, the grains can be refined and the grain area can be increased to reduce the amount of chromium carbide precipitation per unit area of the grain boundary. Chromium is more soluble in ferrite, and Cr23C6 is preferentially formed in ferrite, rather than making the austenite grain boundary poor in chromium; walking the ferrite between austenite can prevent corrosion along the grain boundary to the inside diffusion.
c. Control the residence time in the sensitization temperature range. Adjust the welding heat cycle to shorten the residence time of 600 ~ 1000 ℃ as much as possible, choose the welding method with high energy density (such as plasma argon arc welding), choose a smaller welding line energy, use argon gas on the back of the weld or use copper pad Increase the cooling speed of the welded joint, reduce the number of arc starting and closing times to avoid repeated heating, and the contact surface with the corrosive medium during the multi-layer welding should be welded as far as possible.
d. After welding, solid solution treatment or stabilization annealing (850 ~ 900 ℃) is carried out and air-cooled after heat preservation, so that the carbide can be analyzed and the chromium can be accelerated to diffuse).
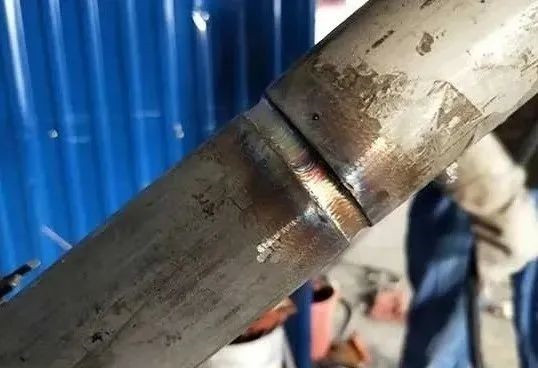
(2). Knife-shaped corrosion of welded joints. For this reason, the following preventive measures can be taken:
Due to the strong diffusion capacity of carbon, during the cooling process, it will segregate at the grain boundary to form a supersaturated state, while Ti and Nb remain in the crystal due to the low diffusion capacity. When the welded joint is heated again in the sensitization temperature range, supersaturated carbon will precipitate out in the form of Cr23C6 between the crystals.
a. Reduce carbon content. For stainless steel containing stabilizing elements, the carbon content should not exceed 0.06%.
b. Use reasonable welding process. Choose a smaller welding line energy to reduce the residence time of the overheated zone at high temperature, and pay attention to avoid the "medium temperature sensitization" effect during the welding process. In double-sided welding, the weld that comes into contact with the corrosive medium should be welded last (this is the reason why the large-diameter thick-walled welded pipe is welded after the outer welding). If it cannot be implemented, the welding specification and the shape of the weld should be adjusted to avoid The overheated area in contact with the corrosive medium is again sensitized and heated.
c. Post-weld heat treatment. After welding, solid solution or stabilization treatment.
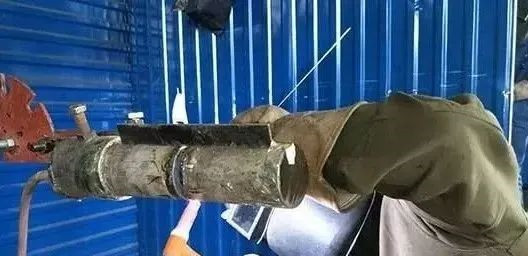
02 Stress corrosion cracking
The following measures can be taken to prevent stress corrosion cracking:
a. Correct selection of materials and reasonable adjustment of weld composition. High purity chromium-nickel austenitic stainless steel, high silicon chromium-nickel austenitic stainless steel, ferrite-austenitic stainless steel, high chromium ferritic stainless steel, etc. have good resistance to stress corrosion, and the weld metal is austenitic The structure of austenite-ferrite dual phase steel has good stress corrosion resistance.
b. Eliminate or reduce residual stress. Conduct stress relief heat treatment after welding, and use mechanical methods such as polishing, shot peening and hammering to reduce the residual stress on the surface.
c. Reasonable structural design. In order to avoid large stress concentration.
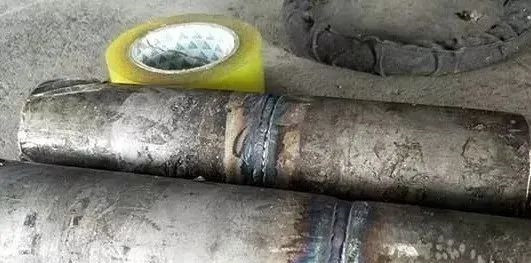
03 Welding thermal cracks (crystallization cracks in the weld, liquefaction cracks in the heat affected zone)
The thermal cracking sensitivity mainly depends on the chemical composition, structure and performance of the material. Ni easily forms low melting point compounds or eutectic with impurities such as S and P, and segregation of boron and silicon will promote thermal cracking.
Welds are prone to form coarse columnar crystal structures with strong directionality, which is beneficial to the segregation of harmful impurities and elements. This promotes the formation of a continuous intergranular liquid film and improves the sensitivity to thermal cracking. If the welding is not heated uniformly, it is easy to form large tensile stress and promote the generation of welding hot cracks.
Preventive measures:
a. Strictly control the content of harmful impurities S and P.
b. Adjust the structure of the weld metal. The two-phase structure weld has good crack resistance. The δ phase in the weld can refine the grains, eliminate the directionality of single-phase austenite, reduce the segregation of harmful impurities at the grain boundary, and the δ phase can dissolve more. S, P, and can reduce the interface energy, the formation of intercrystalline liquid film.
c. Adjust the composition of the weld metal alloy. In the single-phase austenitic steel, the content of Mn, C, and N is appropriately increased, and the addition of a small amount of trace elements such as cerium, pick, and tantalum (which can refine the weld structure and purify the grain boundaries) can reduce the thermal crack sensitivity.
d. Process measures. Minimize the overheating of the molten pool to prevent the formation of coarse columnar crystals. Use small line energy and small cross-section weld beads. For example, 25-20 austenitic steel is prone to liquefaction cracks. By strictly limiting the impurity content and grain size of the base material, high energy density welding methods, small line energy, and improved joint cooling rate can be adopted.
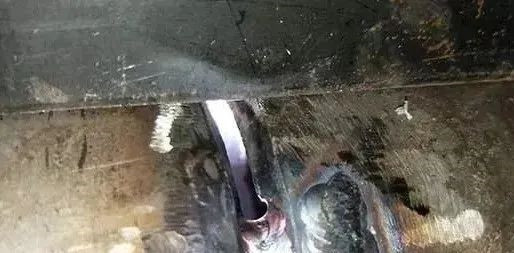
04 Brittleness of welded joints
Hot-strength steel should ensure the plasticity of the welded joint to prevent embrittlement at high temperature; low-temperature steel requires good low-temperature toughness to prevent low-temperature brittle fracture of the welded joint.
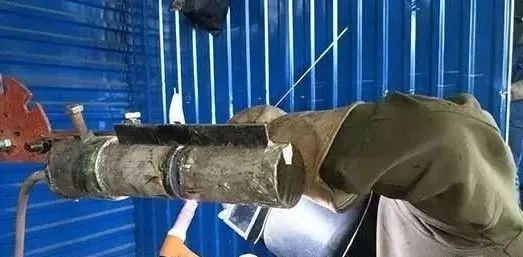
05 Large welding distortion
Due to the low thermal conductivity and large expansion coefficient, the welding deformation is large, and a clamp can be used to prevent deformation. Austenitic stainless steel welding method and welding material selection:
Austenitic stainless steel can be welded by tungsten arc welding (TIG), melting electrode argon arc welding (MIG), plasma argon arc welding (PAW) and submerged arc welding (SAW).
Austenitic stainless steel has low welding current because of its low melting point, small thermal conductivity and large resistance coefficient. Narrow welds and narrow welds should be used to reduce high-temperature residence time, prevent carbide precipitation, reduce weld shrinkage stress, and reduce hot crack sensitivity.
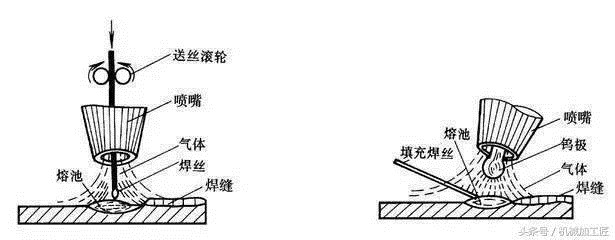
1. The composition of welding materials, especially Cr and Ni alloy elements, is higher than that of the base material. Welding materials containing a small amount (4 to 12%) of ferrite are used to ensure good crack resistance (cold cracking, hot cracking, stress corrosion cracking) of the weld.
2. When the ferrite phase is not allowed or impossible in the welding seam, the welding consumables should use welding materials containing Mo, Mn and other alloy elements.
3. The C, S, P, Si and Nb in the welding consumables should be as low as possible. Nb will cause solidification cracks in pure austenitic welds, but a small amount of ferrite in the welds can be effectively avoided.
4. Welding structures that need to be stabilized or stress-relieved after welding are usually welded with Nb. Submerged arc welding is used for welding medium plates, and the burning loss of Cr and Ni can be supplemented by the transition of flux and alloying elements in the welding wire;
5. Due to the large penetration depth, care should be taken to prevent the generation of thermal cracks in the center of the weld and reduce the corrosion resistance in the heat affected zone. Care should be taken to select thinner welding wire and smaller welding line energy. The welding wire needs to have low Si, S and P.
6. The ferrite content in heat-resistant stainless steel welds should not exceed 5%. For austenitic stainless steels with Cr and Ni contents greater than 20%, high Mn (6-8%) welding wire should be used, and alkaline or neutral flux should be used as the flux to prevent Si from being added to the weld to improve its crack resistance.
7. Austenitic stainless steel special flux has very little added Si, can transition alloy to the weld, and compensate the burning loss of alloy elements to meet the requirements of weld performance and chemical composition.