Process characteristics of vanadium steel
Process characteristics of vanadium steel
Since Henry Ford I of the United States first applied vanadium steel to automobiles and greatly improved the performance of automobiles, people quickly realized the various excellent properties of vanadium steel. In addition to automobiles, vanadium steel has also been widely used in other fields. The output has increased rapidly, and the consumption of vanadium has increased, and the consumption of vanadium per million tons of steel products has reached 35 to 45 tons. In order to obtain good performance vanadium steel and give full play to the performance potential of vanadium steel, some process characteristics of vanadium steel must be fully understood when producing vanadium steel.
①Low reheating temperature
Since vanadium carbonitrides have high solubility in austenite, V(C,N) can be completely dissolved at a lower reheating temperature during reheating. The calculation of the solid solubility product formula shows that even when vanadium When the content is 0.05% and the nitrogen content is 0.02%, the complete solid solution temperature of VN is only 1140℃, so a lower soaking temperature can be used in actual production. On the contrary, the solid solution temperature of niobium steel is relatively high, and it needs to be heated to 1200℃ to completely dissolve the carbonitride of niobium. The relatively high solubility of vanadium steel, especially the higher solubility of carbides, is very important for heat-treated steel, because it ensures that most of the alloying elements can be dissolved at the heat treatment temperature, and can be precipitated during cooling. Only in this way can the precipitation strengthening be fully produced and the purpose of improving the strength can be achieved.
During reheating, austenite grain coarsening occurs in any steel. The higher the reheating temperature, the more obvious the coarsening of the original austenite grains. Therefore, the use of a lower reheating temperature is beneficial to suppress the original austenite The coarsening of bulk grains, vanadium steel just has such favorable conditions. At a lower reheating temperature, such as 1150°C, all the carbonitrides of vanadium can be dissolved, which is good for refining the original austenite grains. It is very advantageous. Studies have shown that using a lower reheating temperature can suppress the abnormal coarsening of the original austenite grains, and has a significant effect on the refinement of the final structure and the improvement of steel toughness. Many low temperature steels and steels requiring high toughness also use lower reheating temperatures.
②Small resistance to thermal deformation
Among the three main microalloying elements of niobium, vanadium and titanium, vanadium steel has the weakest ability to hinder recrystallization during high-temperature rolling, and the recrystallization termination temperature is relatively low, so the rolling resistance during hot rolling is relatively small, as shown in Figure 1. Show. It can be seen from the figure that as the temperature decreases, the flow stress of vanadium steel increases slowly. Similar to C-Mn steel, it is relatively easy to deform during rolling and has no special requirements for the rolling mill. But the situation of niobium steel is different. As the temperature decreases, the flow stress of niobium steel increases, especially when the temperature is lower than 930℃, the flow stress increases sharply. Niobium has the ability to strongly hinder the recrystallization of austenite, which accumulates the deformation of each pass during rolling, which leads to work hardening, and the rolling resistance is significantly increased. The old rolling mill is no longer applicable, and a new rolling mill with greater rolling force must be used. . Small thermal deformation resistance is another main technological feature of vanadium steel.
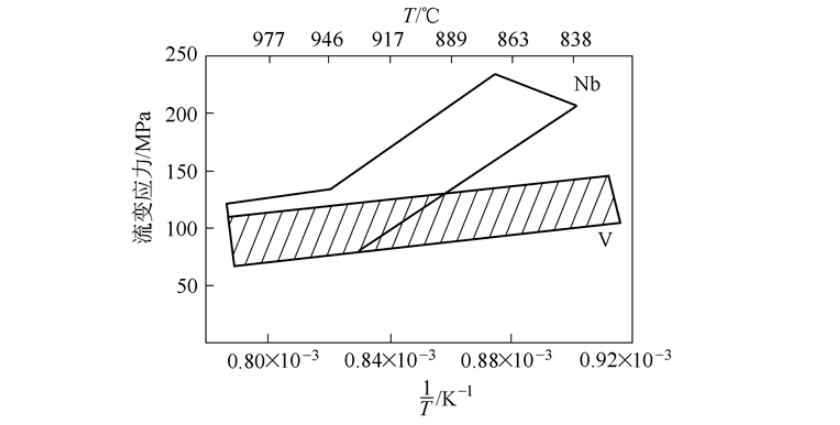
Figure 1 The relationship between flow stress of vanadium steel and final rolling temperature
③The final rolling temperature has little effect on performance
Vanadium in steel is a good precipitation strengthening element. Even at a higher final rolling temperature, better toughness can be obtained. This is due to the fact that vanadium steel passes through more reciprocating rolling in the austenite recrystallization zone. The secondary rolling-recrystallization deformation process can finally obtain finer austenite grains, with a limit value of about 20μm. The high or low final rolling temperature has little effect on the grain size of the austenite after repeated recrystallization. . Therefore, Mitchell once pointed out: When vanadium steel is recrystallized, the grain size of recrystallized austenite tends to maintain a constant value in a wide temperature range. The vanadium-containing HSLA steel has relatively little performance change in the final rolling temperature range of 800~1000℃. This is another technological feature of vanadium steel. The use of a higher final rolling temperature creates favorable conditions for the thickness tolerance of vanadium steel plates, especially for the shape control of high-strength steel strips with a width greater than 1500 mm and a thickness less than 3 mm. Niobium steel does not have this feature. Compared with niobium steel, vanadium steel is more suitable for continuous production of modern high-efficiency rolling mills, shortening and saving rolling time, and greatly improving production efficiency.
④ Adapt to the higher nitrogen content of electric furnace steel
In the case of electric furnace steelmaking, the temperature of the arc zone is relatively high, and the atmosphere in the furnace is connected to the air. High-temperature molten steel is easier to absorb the nitrogen in the atmosphere, which increases the nitrogen content of the molten steel; under the action of the arc , Nitrogen molecules near the arc easily dissociate into nitrogen atoms. The dissolution rate of nitrogen atoms in molten steel is higher than the dissolution rate of molecular nitrogen, which makes the nitrogen content of electric furnace steel higher than that of the converter; the electric furnace steelmaking time is relatively long, and the partial pressure of nitrogen in the furnace is relatively high, which will also cause The nitrogen content increases; in the case of converter steelmaking, not only the smelting time is shorter, but the amount of decarburization is relatively large. While decarburization, it also has a better denitrification effect, so that the nitrogen content of the converter steel is relatively low. Generally, the nitrogen content of converter steel fluctuates in the range of 0.003% to 0.006%. The nitrogen content of electric furnace steel fluctuates in the range of 0.008% to 0.012%, which is 2 to 3 times the nitrogen content of converter steel.
Nitrogen in steel is generally considered a harmful impurity element. Free nitrogen solid solution in ferrite is harmful, it improves the aging sensitivity and brittleness tendency of steel; in continuous ingot, higher nitrogen content can increase the possibility of longitudinal or transverse cracking; in the welding process Among them, free nitrogen will reduce the toughness of the weld and increase the ductility/brittle transition temperature.
To suppress the harmful effects of nitrogen in steel, the most commonly used method is to add an appropriate amount of nitrogen fixation elements, such as aluminum, titanium, and vanadium, to the steel. Among these nitrogen fixing elements, vanadium is the most effective. Vanadium is the only element that has a dual effect on nitrogen. It not only fixes free nitrogen in steel by forming VN or nitrogen-rich V (C, N), and inhibits the harmful effects of nitrogen. And it can also produce significant precipitation strengthening and grain refinement. In particular, it should be pointed out that the use of nitrogen can make the precipitated particles be finely dispersed in the steel to optimize the precipitation strengthening, as shown in Figure 2. It can be seen from the figure that with the increase of nitrogen content, the size of precipitated particles decreases, the volume fraction of precipitated phase increases, the spacing of precipitated particles decreases, and precipitation strengthening increases significantly. Nitrogen plays a very large role in precipitation strengthening. Therefore, nitrogen in vanadium steel has been transformed from a harmful "impurity element" into an indispensable "microalloying element".
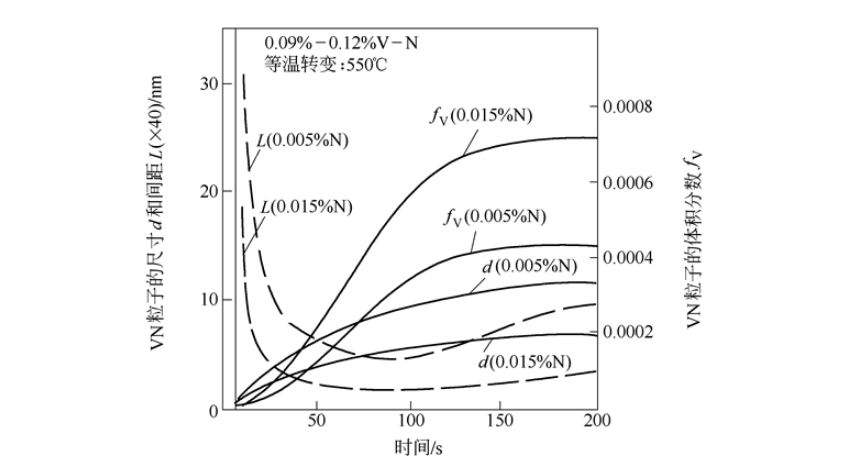
Figure 2 The effect of nitrogen on the size d, volume fraction fV and spacing L of precipitated particles
According to the characteristics of the electric furnace steelmaking process, the electric furnace steel will naturally bring a higher nitrogen content of 0.008% ~ 0.012%, which is equivalent to not adding other additional process measures, not increasing any costs, and freely gifting alloy elements. This is exactly vanadium. What you need for steel. In some cases, the nitrogen content of electric furnace steel needs to be slightly increased, thereby eliminating various denitrification refining processes and reducing the production cost of steel. The above facts show that V-N microalloying has strong adaptability to electric furnace steels with high nitrogen content, which is another outstanding feature of vanadium-containing steels.
What should be pointed out here is the effect of nitrogen content on niobium-containing steel. When the nitrogen content in the niobium-containing steel is high, large-size niobium nitrides may precipitate in the molten steel and reduce the activity and apparent concentration of niobium carbides. At the same time, from the perspective of solubility, the solubility of niobium nitride is lower than that of niobium carbide. When molten steel is solidified, it is easier to precipitate large and harmful niobium nitrides in the solidification front, which significantly reduces the fracture toughness, fatigue strength and thermoplasticity of steel, and limits the full use of the strain-induced precipitation strengthening and grain refinement effects of NbC. Play. It can be roughly considered that when niobium is added to steel, only niobium that forms fine and dispersed NbC or Nb(C,N) particles is effective niobium, and niobium that forms large-size NbN is invalid niobium. In order to avoid the formation of large-scale niobium nitrides, methods such as vacuum refining must be used to greatly reduce the nitrogen content in steel. In a sense, the role of niobium in steel depends on the nitrogen content in the steel on the one hand; on the other hand, in order to prevent the formation of large-scale niobium nitrides at the solidification front, it can also be used to reduce the sulfur, Segregation element content such as phosphorus and other means. Because in the macro-segregation zone, segregated elements such as sulfur and phosphorus are easily enriched in the solidification front, which significantly reduces the solidification temperature of molten steel and promotes the precipitation of large-size NbN. Only by controlling the content of sulfur and phosphorus to the lowest possible level can it be possible to prevent the precipitation of large-size NbN. Therefore, it can be considered that increasing the solidification temperature of molten steel by reducing the content of segregated elements such as sulfur and phosphorus is an effective method to prevent the formation of large-scale NbN precipitation in the macro-segregation zone. For this reason, higher requirements are put forward on the content of impurity elements in niobium-containing steel. According to experience, in low carbon steel (ω(C)<0.1%) the sulfur content should be controlled below 0.01%, and the phosphorus content should be controlled below 0.015%; in medium carbon and high carbon steel (ω(C)>0.1 %) The sulfur content should be controlled below 0.005%, and the phosphorus content should be controlled below 0.01%. Using vacuum refining and other means, the above requirements for impurity elements can be achieved, but this will lead to higher production costs. For niobium steel, nitrogen is a very harmful impurity element.