Natural Gas Pipelines
Natural Gas Pipelines
Basic knowledge compilation of Natural Gas Pipelines
With the increasing efforts of my country's natural gas exploration and development and the increasing material and environmental needs of the people, the development of long-distance natural gas pipelines has been very rapid in recent years. With the continuous extension of pipelines, the social, political and economic responsibilities of pipeline companies have become greater. Therefore, it is particularly important to popularize knowledge about natural gas long-distance pipelines.
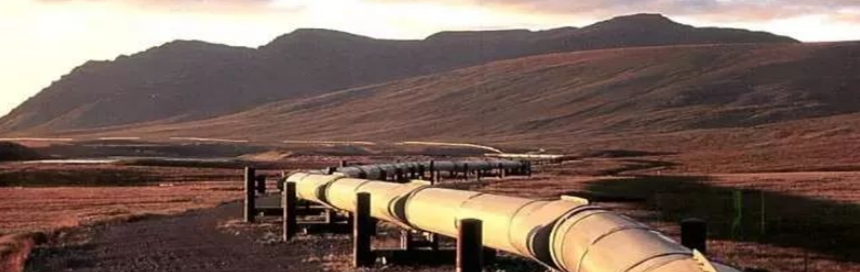
One. Line engineering
Gas pipeline engineering refers to the engineering of natural gas and coal gas by pipeline, which generally includes gas transmission lines, gas transmission stations, pipeline crossing (span) and auxiliary production facilities.
The line project is divided into main gas transmission lines and branch gas transmission lines. The main gas transmission line is the main operating pipeline from the first gas transmission station to the final gas transmission station; the gas branch line is the pipeline that transports gas to the main gas transmission line or the output pipe of the gas transmission main line.
The line cutoff valve chamber is part of the line project. The main equipment includes pigging tee, line cutoff ball valve, upstream and downstream venting bypass process, venting riser, etc. The function is to segment the line under extreme conditions or line maintenance. Truncated. The valve chambers are arranged at different intervals according to the different grades of the regions through which the line passes.
The valve chamber system includes two categories: manual valve chamber and RTU valve chamber.
1. Manual valve chamber
The manual valve chamber realizes automatic shut-off of overpressure, low pressure, and pressure drop rate detection and local indication of process parameters in the valve chamber. The main local measurement and control parameters are: pipeline temperature display, and pressure display before and after the emergency shut-off valve.
2. RTU valve chamber
The RTU system realizes remote data collection, monitoring and management of the process in the valve chamber, as well as monitoring and alarming of combustible gas leakage.
Main functions of RTU system:
1) Data collection and transmission function: collect process operating parameters in the valve chamber and transmit them to the control center system.
2) Control function: execute instructions issued by the control center; start and stop control of the entire valve room; remote control of line gas-liquid linkage valves and local manual control.
3) Other functions: self-diagnosis and self-recovery; exchange information with third-party systems or smart devices via the communication interface.
Two. Craft station
Gas transmission station is a general term for all kinds of process stations in gas transmission pipeline engineering. Generally, it includes stations such as the first gas transmission station, the last gas transmission station, the gas compressor station, the gas receiving station, the gas distribution station, and the pigging station.
The gas transmission station is an important part of the gas pipeline system, and its main functions include pressure regulation, filtration, metering, pigging, pressurization and cooling. The purpose of pressure regulation is to ensure that the input and output gas has the required pressure and flow; the purpose of filtration is to remove solid impurities in natural gas, avoid increasing gas transmission resistance, wear instrument equipment, and pollute the environment; metering is gas It is indispensable for sales and business transfer, and it is also the basis for automatic control of the entire pipeline; the purpose of pigging is to remove debris and dirt in the gas pipeline, improve pipeline transmission efficiency, and reduce friction loss and pipeline inner wall Corrosion, prolong the service life of the pipeline; the purpose of pressurization is to provide a certain pressure energy for natural gas; and cooling is to reduce the temperature of the gas due to the increase in pressurization to ensure the efficiency of gas transmission. Depending on the location of the gas transmission station, their respective roles are also different.
1. First stop
The first station is the starting point of the gas pipeline. The first station of gas transmission is generally near the gas field, and the first station of the Sichuan-East Gas Pipeline is adjacent to the Puguang Gas Field.
The main functions of the first station:
——Receive the gas from the natural gas purification plant and conduct online gas quality analysis and chromatographic analysis;
——Filtering and separating natural gas;
——Measuring and online calibration of the filtered natural gas;
——The metered natural gas is sent to the downstream station after being pressurized or bypassed;
——Pig delivery;
-Emergency cut off;
——The state of the accident and the emptying and drainage during maintenance;
——Data collection and monitoring of station yard.
2. Last stop
The last station is the terminal station of the gas pipeline. The gas passes through the terminal and is supplied to the user. Therefore, the terminal station has functions such as pressure regulation, filtration, metering, and pig acceptance. In addition, in order to solve the problem of pipeline transportation and user gas imbalance, there are also peak shaving facilities, such as underground gas storage, gas storage tanks, etc. The Sichuan-East Gas Pipeline has six dedicated lines and branch terminal stations, namely: Dahua terminal station, Chuanwei terminal station, Jiujiang terminal station, Yangzi Petrochemical terminal station, Nanjing terminal station, Jinling terminal station; the main trunk line terminal station One is the last station in Shanghai.
The main functions of the last station:
——Pig receiving;
——Gas filtration and separation treatment;
——Gas flow measurement and online calibration;
——Gas pressure regulation;
-Self-use gas supply in the station;
-Emergency cut off and emptying of the station yard;
——Sewage discharge from the station;
——Data collection and monitoring of station yard.
3. Pigging station
The pigging station is a process station with the functions of pig receiving and sending, natural gas separation equipment and facilities and pigging operations. A total of 2 stations with pure pigging function are set up along the Sichuan-East Gas Pipeline, which are respectively set up at Huangjin and Yesanguan, and the pipeline is regularly pigged in sections.
The main functions of the pigging station:
——Pig receiving and sending;
——The main line gas cyclone separation;
-Self-use gas supply in the station;
-Emergency cut off and emptying of the station yard;
——Data collection and monitoring of station yard.
4. Compressor station
A compressor station is a station set up along the gas pipeline to pressurize the pipeline gas with a compressor. There are three compressor stations in the Sichuan-East Gas Pipeline, namely Puguang First Station, Lichuan Compressor Station, and Qianjiang Compressor Station.
The main functions of the compressor station:
——Receive the gas from the purification plant and conduct online gas quality analysis and chromatographic analysis;
——Filtering and separating natural gas;
——Measuring and online calibration of the filtered natural gas;
——The metered natural gas is sent to the downstream station after being pressurized or bypassed;
——Pig delivery;
-Emergency cut off;
——The state of the accident and the emptying and drainage during maintenance;
——Data collection and monitoring of station yard.
5. Substation
Along the gas pipeline, stations set up to distribute gas to users generally have functions such as separation, pressure regulation, metering, and pigging.
6. Gas receiving station
Along the gas pipeline, the stations set up to receive gas from the branch gas pipeline generally have the functions of separation, pressure regulation, metering, and pigging.
Three. Automatic control system
With the development of electronic computers, instrument automation technology, communication technology and information technology, the "Supervisory Control And Data Acquisition (SCADA system)" has been widely used to complete the automatic monitoring and automatic monitoring of natural gas pipeline transportation. Protection has become the basic mode of pipeline automatic control system. The automatic control system of the Sichuan-East Gas Pipeline Project uses a computer-centric monitoring and data acquisition (hereinafter referred to as SCADA) system.
Under normal circumstances, the dispatch control center is responsible for the entire line of automated control and dispatch management. In the event of a dispatch control center failure or war, natural disasters, etc., the backup control center takes over the full line of SCADA system monitoring.
The pipeline SCADA system implements long-distance data collection, monitoring and control, security protection and unified dispatch management for each station. The dispatch control center can issue dispatch instructions to each station control system, and the station control system completes the control function; the dispatch control center realizes resource sharing, real-time collection and centralized processing of information through the communication system. The Sichuan-East Gas Transmission Pipeline adopts a three-level control method of the entire line dispatch center control level, station control level and local control level.
The first level is the central control level: remotely monitor the entire line and implement unified dispatch management. Under normal circumstances, the dispatch control center monitors and controls the entire line. The control of stations along the line does not require manual intervention, and the SCS and RTU of each process station will complete their monitoring work under the unified command of the dispatch control center.
The second level is the station control level: at the first station, each sub-transmission station, compressor station, and last station, the station control SCS system performs data collection, monitoring and control, and interlocking protection for the process variables and equipment operating status in the station. Set up a remote terminal unit (RTU) at an unattended pigging station to collect, monitor and control process variables and equipment operating status in the station. The control authority of the station yard control level is determined by the dispatch control center. Only after the dispatch control center is authorized, the operators are allowed to operate within the authorized scope of each station through SCS or RTU. When the communication system fails or the system is overhauled, the station control system is used to monitor and control each station.
The third level is the local control level: the local control system performs manual/automatic local control of the process monomer or equipment. When the equipment is overhauled or emergency cut off, local control can be used.
SCADA system configuration and functions:
1. Dispatch control center
The configuration hardware part includes various servers and workstations, and the software part includes operating system software, SCADA system software, database management, alarm and event management, and special software packages (receiving ball tracking, simulation software and gas management system (GMS) software, etc. ).
The main functions include: data collection and processing; issuing scheduling and operating commands; displaying dynamic process flow; alarm and event management; historical data collection, archiving and trend display; report generation and printing; standard configuration software and user-generated applications Software execution; clock synchronization; capable of real-time simulation of gas transmission process and training of operators; pressure and flow adjustment; gas transmission process optimization; fault diagnosis and analysis of instruments and systems; network monitoring and management; main-standby communication Automatic switching of channels; trade settlement management; emergency shutdown of the whole line; pipeline leakage detection.
2. Backup control center
The configuration hardware part includes various servers and workstations, and the software part includes operating system software, SCADA system software, database management, alarm and event management, and special software packages (receiving ball tracking, simulation software and gas management system (GMS) software, etc. ).
The main functions include: data collection and processing; issuing scheduling and operating commands; displaying dynamic process flow; alarm and event management; historical data collection, archiving and trend display; report generation and printing; standard configuration software and user-generated applications Software execution; clock synchronization; pressure and flow adjustment; fault diagnosis and analysis of instruments and systems; network monitoring and management; automatic switching of main and standby communication channels; emergency shutdown of the whole line; pipeline leakage detection.
3. Monitoring terminal of gas transmission management office
The management office is equipped with two monitoring terminals respectively, which can only realize data monitoring but not control.
The main functions of the monitoring terminal are as follows: dynamic process flow display; alarm and event display; trend display of historical data; fault diagnosis and analysis display of the instrument.
4. Station control system
Each station is equipped with SCS, with different numbers of workstations, station control system PLC, and ESD system PLC.
The station control system completes the following main functions: data collection and transmission functions, control functions, display functions, printing functions, ESD shutdown functions, data management and other functions.
5. Remote control terminal RTU
The whole line is equipped with remote control line cutoff valve room RTU, RTU can achieve the following main functions: data acquisition and processing; logic control; receiving instructions sent by the dispatch control center; sending real-time data with time stamps to the dispatch control center; self-diagnosis function; fault Call the police.
6. Flow measurement and trade management
1) Trade measurement
The custody transfer flowmeter uses gas ultrasonic flowmeter or gas turbine flowmeter. The diameter of turbine flowmeter is generally smaller than DN100. The gas ultrasonic flowmeter is between 5%Qmax~Qmax (Qmax is the inherent maximum flow range of the flowmeter) to ensure that the measurement accuracy is better than ±0.5%. The gas turbine flowmeter guarantees measurement accuracy better than ±0.5% within the range of 20% qmax~qmax; the gas turbine flowmeter guarantees measurement accuracy better than ±1% within the range of qmin~20% qmax. The metering system uses an independent flow computer as the flow accumulation unit and transmits the data to the SCS system.
The first station is to set up online chromatogram, H2S and water dew point analyzers to detect natural gas quality and parameters.
Other metering stations are equipped with online chromatographic analyzers to detect the quality and parameters of natural gas.
The dispatch control center is equipped with a gas management system (GMS) to calculate on-site natural gas flow, temperature, and pressure data, and provide data for the trade management system.
2) Self-consumption gas metering
Install the self-consumption gas processing skid in the station yard, and adopt the turbine flowmeter for self-consumption gas measurement. Self-consumption gas at the station includes gas for venting torch ignition, gas for natural gas generators and domestic gas.
7. Gas Management System (GMS)
The gas management system (GMS) is a gas volume/energy trade management system that can automatically manage the transfer, sales and transmission of natural gas, provide the required data for the company's finances, provide the data required for user inquiries, and complete the functions required for trade settlement And archive the data.
The gas management system (GMS) software structure is divided into the following parts: real-time data and historical database management platform, pipeline operation plan, management and financial information system, gas measurement system, etc.
8. Simulation system
To accurately evaluate the pipeline's past, explain the current events of the pipeline, and predict the future of the pipeline. The Sichuan-East Gas Pipeline adopts real-time simulation software to provide dispatching and operation reference for operators and dispatchers, and provides a platform for operator training to ensure safe, stable, efficient and economical operation of the gas pipeline.
The simulation software configures the pipeline model according to the actual situation of the pipeline. Calculate the results according to needs, such as pipeline leakage alarm, natural gas component tracking, flow rate of each pipe section, pipe gas storage, pressure distribution status, position of the pig in the pipeline, etc., written into SCADA by simulation software In the real-time database, and displayed on the operator's workstation, as the operator's reference for pipeline operation scheduling.
The simulation system includes: real-time transient, hydraulic characteristics, gas component tracking, instrument analysis, pipe charging management, pipeline efficiency, pig tracking, process prediction, SCADA training, etc.
Frou. Communication system
The communication system is to provide a variety of communication services for the production scheduling, administrative management, rush repairs, and life logistics of the long-distance pipeline, open remote monitoring and video services such as conference TV, and provide a reliable channel for the data transmission of the pipeline SCADA system. Digital pipelines provide communication support. Due to the high degree of automation of the long-distance pipeline construction and the few maintenance personnel, the communication system is required to be advanced in technology, stable and reliable, and high in transmission quality, so as to minimize the daily maintenance workload and be able to meet the needs of future communication development.
The general pipeline communication part includes: optical transmission system, TV monitoring system and perimeter security system, video conference system, program-controlled telephone exchange system, local area network office automation (OA) system, line inspection and emergency communication system and public network backup communication system, etc. Seven parts.
Communication realization methods generally adopt optical fiber communication, DDN public network communication, GPRS wireless communication and satellite communication.
Five. Power supply and distribution system
1. Station power supply and distribution
For stations with heavy power loads such as gas compressor stations, 110 kV or 35kV substations shall be constructed to provide power. Other stations with relatively small power loads generally report the installation of 10 kV external power lines, and the power supply is provided by a 10 kV /0.4 kV transformer.
In order to ensure the normal operation of gas transmission and production, an automated natural gas generator set is selected as the emergency self-provided power source. In the event of an external power failure, the generator set shall provide power for the primary and secondary loads in the station. Rated voltage selection of natural gas generator set: AC 380/220V, 50Hz, 3-phase, 4-wire. The operation mode is automatic switching between mains and power generation.
2. Power supply and distribution of valve room system
(1) RTU valve room power supply
RTU valve room power supply mainly includes three methods: external power supply, solar power system and small-capacity gas power generation device.
According to the geographic location of the RTU valve room, a solar power system and a small-capacity gas power generation device are respectively set up to provide power for the automatic control, communication, anti-corrosion and lighting in the RTU valve room. The use of solar power to power the valve chamber is mainly based on the similar weather conditions where the RTU valve chamber is located, and it is determined that solar power is used in plain areas and where there is no sun shade when there is no light day less than or equal to 11 days. The valve room uses 1000Ah valve-controlled sealed lead-acid battery as a backup power source, with a backup time of about 48 hours, and realizes remote monitoring and control through the SCADA system. All alarm signals are transmitted to the SCADA system through the common alarm contact.
The RTU valve room powered by the external power supply adopts a 10kV high-voltage external power supply, a 10/0.4kV substation and distribution room is built in the station, and a single indoor dry-type transformer. In order to meet the requirements of the first-level power load, the configuration ensures that the external power supply loses power In the case of using redundant UPS uninterruptible power supply, the uninterrupted time is 3 days considering the battery configuration. At the same time, the power supply device has local and remote monitoring functions.
(2) Power supply for manual valve chamber
The power demand of the manual valve chamber is mainly to meet the electronic control unit of the line cut-off valve chamber actuator. The power load is very small. It is powered by small solar panels and sealed lead-acid batteries. In the case of sunlight, solar power supplies the lead-acid batteries. For floating charge, the normal operating voltage of the electronic control unit of the actuator is maintained by the lead-acid battery.
Six, pipeline anticorrosion
1. Anticorrosion of line and pipeline
(1) Line pipelines generally adopt a combination of external anti-corrosion layer and cathodic protection. Three-layer PE is used for the outer anticorrosive coating of the pipeline, and the cathodic protection adopts forced current cathodic protection, and cathodic protection stations are set up along the line according to the protection distance requirements.
The cathodic protection design parameters are as follows:
Natural potential: -0.55V (relative to saturated copper sulfate reference electrode)
Confluence point potential: -1.15V (relative to saturated copper sulfate reference electrode)
Minimum protection potential of pipeline: -0.85 V (relative to saturated copper sulfate reference electrode)
Pipeline protection current density: 5μA/m2
Design life: 30 years
External anti-corrosion coating for gas transmission: three layers of PE
(2) The basic situation of external replenishment:
Ø Solvent-free liquid epoxy coating + heat shrinkable patch tape is used for the patch of three-layer PE and the patch of simmering elbow in general pipe section.
Ø The reinforced 3-layer PE patch of the directional drill crossing section is made of solvent-free liquid epoxy coating + special heat shrinkable patch tape for directional drilling.
(3) Internal coating of line and pipeline
Generally, the inner surface of the main pipeline adopts two-component liquid epoxy coating, and the dry film thickness is ≥65μm.
In order to improve the performance of the cathodic protection system of the long-distance pipeline and the effective protection of the pipeline, an independent cathodic protection monitoring system can be adopted, with intelligent test piles set up at key locations along the line, and potential collectors in the RTU valve room. The intelligent test pile uses GPRS communication method, uses long-life battery power supply, uses low power consumption technology to complete the GPRS communication radio location collection function, and automatically GPRS connection and data transmission. The RTU valve chamber potential collector uses optical cables for data transmission. The cathodic protection monitoring center is located in the main control center.
2. Anticorrosion of valve chamber process pipeline
The part connecting the valve chamber process and the main line adopts forced current cathodic protection; the valve chamber vent system is equipped with an insulating joint, and the cathodic protection method of sacrificial anode is adopted.
(1) The outer surface of the above ground natural gas pipeline, venting pipeline, and venting standpipe
Primer: epoxy zinc-rich primer, 2 coats, 80~100mm
Intermediate paint: epoxy mica intermediate paint, 1 coat, 100mm
Finish: Acrylic polyurethane finish, 2 coats, 80~100mm
Total dry film thickness ≥260mm
(2) The outer surface of the buried pipeline
Primer: epoxy zinc-rich primer, 2 coats, 80~100mm
Finish: solvent-free liquid epoxy paint, 1 coat, 500mm
Total dry film thickness ≥580mm
3. Anti-corrosion of station process pipeline
For pipeline technology stations, general booster stations use forced current cathodic protection; other stations use sacrificial anode cathodic protection, with insulated joints for incoming and outgoing pipelines.
(1) The outer surface of the above-ground process pipeline
Primer: epoxy zinc-rich primer, 2 coats, 80mm
Top coat: epoxy siloxane top coat, 1 coat, 125mm
Total dry film thickness ≥205mm
(2) The outer surface of the buried process pipeline
Primer: epoxy zinc-rich primer, 2 coats, 80mm
Finish: solvent-free liquid epoxy paint, 1 coat, 500mm
Total dry film thickness ≥580mm
Seven, gas storage
Gas consumption is constantly changing, with monthly unevenness, daily unevenness and time unevenness, but the origin of the supply cannot be changed at any time according to the changes in gas consumption, especially for long-distance gas pipelines. To achieve high efficiency and best economic benefits, we always hope to work under a certain optimal output. In this way, there is often an imbalance between gas supply and gas consumption. In order to ensure uninterrupted gas supply according to user requirements, the balance between gas production and use must be considered.
There are three ways to solve the imbalance between gas consumption and gas supply:
Ø Change the production capacity of the gas source and set up a mobile gas source;
Ø Use buffer users to play the role of scheduling;
Ø Use various gas storage facilities.
The first two points are restricted by the possibility and range of changes in the production load of the gas source, as well as the safety and reliability of the gas supply and the technical and economic rationality requirements, and it is impossible to completely solve the imbalance between supply and demand. Due to the flexibility of gas storage facilities and methods, the use of various gas storage facilities is one of the most effective methods to solve the unevenness of gas consumption. According to the storage method, gas storage is divided into: underground storage, gas tank storage, liquid or solid storage, and gas storage pipeline end storage.