Duplex Stainless Steel Processing and Manufacturing (2)
Practical guide for Duplex Stainless Steel Processing and Manufacturing (2)
The application of duplex stainless steel is becoming more and more extensive, and users are more and more familiar with this type of stainless steel. This article focuses on one of the difficulties of duplex stainless steel application-processing and welding, introduces the various characteristics of duplex stainless steel, and gives the basic principles and practical information for processing and welding duplex stainless steel.
Contents include: history, chemical composition, metallurgy, corrosion resistance, mechanical properties, physical properties, technical conditions, quality control, cutting, forming, welding, and applications of duplex stainless steel.
The full text is longer and will be published in several parts. Welcome to pay attention!
5 Corrosion resistance
In the environment of most standard austenitic stainless steel applications, duplex stainless steels show high corrosion resistance, it is worth noting that they have very obvious advantages in some cases. This is due to their high chromium content, which is very beneficial in oxidizing acids, and contains sufficient amounts of molybdenum and nickel, which can resist the corrosion of medium reducing acid medium.
The relatively high chromium, molybdenum, and nitrogen contents of duplex stainless steels also make them resistant to chloride pitting and crevice corrosion. Their duplex structure is an advantage in environments where chloride stress corrosion cracking may occur.
If the microstructure of duplex stainless steel contains at least 25% to 30% ferrite, its resistance to chloride stress corrosion cracking is far better than that of austenitic stainless steel 304 or 316. However, ferrite is prone to hydrogen embrittlement, so duplex stainless steel has low corrosion resistance in environments or applications where hydrogen may enter the metal, and hydrogen embrittlement will occur.
5.1 Acid corrosion resistance
In order to illustrate the corrosion resistance of duplex stainless steel in strong acid solution, Figure 6 shows the corrosion data of sulfuric acid solution. The media conditions range from a weakly reducing environment with a low acid concentration to a high concentration oxidizing environment and a strong reducing environment with a medium concentration hot solution.
2205 and 2507 duplex stainless steels perform better than many high-nickel austenitic stainless steels in solutions with an acid concentration of up to about 15%; in the range of acid concentrations of at least 40%, duplex stainless steels are superior to 316 or 317 stainless steels.
Duplex stainless steel is also useful in this chloride-containing oxidizing acid.
The nickel content of duplex stainless steel is not enough to withstand the strong reducing corrosion of medium concentration sulfuric acid solution or hydrochloric acid. In a reducing environment, where there is a wet/dry interface where the acid is concentrated, corrosion, especially ferrite corrosion, will begin and progress rapidly.
The resistance to oxidation corrosion of duplex stainless steels makes them excellent candidates for nitric acid and strong organic acid installations.
Figure 7 shows the corrosion of duplex stainless steel and austenitic stainless steel in a mixed solution of 50% acetic acid and formic acid with different contents at the boiling temperature. Although 304 and 316 stainless steels can be used in strong organic acid media at room temperature and medium temperature, 2205 and other duplex stainless steels have advantages in many processes involving high-temperature organic acids, and because they are resistant to pitting and stress corrosion, they are also available Used in halogenated hydrocarbon process.
5.2 Alkali corrosion resistance
The high chromium content of the duplex stainless steel and the presence of the ferrite phase make it have good performance in alkaline media. At moderate temperatures, the corrosion rate is lower than that of standard austenitic stainless steels.
5.3 Resistance to pitting corrosion and crevice corrosion
In order to discuss the stainless steel's resistance to pitting and crevice corrosion, the concept of critical pitting temperature is introduced. For a certain chloride environment, each stainless steel can be characterized by a temperature. Above this temperature, pitting begins to occur, and it can develop to the extent visible to the naked eye within 24 hours. Below this temperature, pitting corrosion will not occur for an infinite period of time. This temperature is called the critical pitting temperature (CPT). It is a characterization of specific stainless steel grades and specific environments. Since the initial occurrence of pitting is statistically random, and CPT is sensitive to small changes in brands and products, CPT for different brands is usually expressed in a temperature range. The research tool introduced by the ASTM G 150 standard, namely the electrochemical measurement method, may be able to accurately and reliably determine CPT.
Crevice corrosion also has a similar critical temperature, called the critical crevice corrosion temperature (CCT). CCT depends on the characteristics of the stainless steel specimen, chloride environment and gap (tightness, length, etc.). Due to the geometry of the gap and the fact that it is difficult to reproduce the size of the same gap, the measurement data of CCT is more dispersed than CPT. Generally, for the same steel and in the same corrosive environment, CCT is often 15-20°C (27-36°F) lower than CPT.
The high chromium, molybdenum, and nitrogen of duplex stainless steels make them very resistant to chloride local corrosion in aqueous environments. Depending on the alloy content, some duplex stainless steel grades even rank among the best performing stainless steels. Duplex stainless steel has a relatively high chromium content, so it has good corrosion resistance and is very economical.
Figure 8 shows a comparison of the pitting and crevice corrosion resistance of some solution annealed stainless steels measured in accordance with ASTM G 48 2 (6% FeCl3). The critical temperature of the welding state of the material is lower. A high critical pitting or crevice corrosion temperature indicates that the material has a higher ability to resist the onset of corrosion. The CPT and CCT of 2205 steel are significantly higher than 316 stainless steel. This makes 2205 steel a versatile material suitable for environments where chloride ions are concentrated due to evaporation and under the steam space or insulation of heat exchangers. The CPT of 2205 duplex steel also shows that it can be used in alkaline water and degassed brine. It is also successfully used in degassed seawater. In these applications, the surface of the steel is free of deposits through high-velocity seawater or other methods.
In demanding applications, such as thin-walled heat exchanger tubes, or deposits or cracks on the surface, 2205 duplex steel does not have sufficient resistance to crevice corrosion in seawater. However, high alloyed duplex stainless steels with a CCT higher than 2205, such as super duplex stainless steels, have been used in many harsh seawater conditions that require both high strength and resistance to chloride ion corrosion.
Because CPT is a function of materials and specific environments, it is possible to study the impact of a single element. Using the CPT determined according to the ASTM G 48 A method, the relationship between the composition of the steel (considering each element as an independent variable) and the measured CPT (correlated variable) is obtained by regression analysis. The results show that only chromium, molybdenum, tungsten and nitrogen have a stable effect on CPT. The relationship is as follows:
CPT = constant + %Cr + 3.3 (%Mo + 0.5%W) + 16%N.
The sum of the four alloy elements in the formula multiplied by their respective regression constants is usually called the equivalent pitting corrosion resistance (PREN). Different researchers give different coefficients of nitrogen, usually 16, 22 and 30. You can sort the brands of a family based on the PRE value, but you should pay attention to avoid excessive dependence on this relationship. The alloying elements in the formula are "independent variables", but they are not really independent, because the steel tested is a balanced composition. This relationship is not linear or cross-linked, for example, the synergistic effect of chromium and molybdenum is ignored. This relationship is only for materials in an ideal state, without considering the effects of intermetallic phases, non-metallic phases, and improper heat treatment. Improper heat treatment also adversely affects corrosion resistance.
5.4 Resistance to stress corrosion cracking
Some of the earliest applications of duplex stainless steels were based on their resistance to chloride stress corrosion cracking (SCC). Compared with austenitic stainless steels that have similar resistance to chloride pitting and crevice corrosion, duplex stainless steels exhibit significantly superior stress corrosion cracking resistance. Many applications of duplex stainless steels in the chemical processing industry replace the use of austenitic stainless steels where there is a high risk of stress corrosion cracking. However, like all other materials, duplex stainless steels are prone to stress corrosion cracking under certain conditions. This situation may occur at high temperatures, in chloride-containing environments, or in the presence of medium conditions that promote hydrogen-induced fractures.
Environmental conditions such as stress corrosion cracking may occur in duplex stainless steels, such as the 42% boiling magnesium chloride solution test, and the droplet evaporation test of the metal at high temperature and exposure to a pressurized aqueous chloride system (the temperature in the system may be higher than that under normal pressure) temperature).
Figure 9 shows the relative chloride stress corrosion cracking resistance of several rolled annealed duplex stainless steels and austenitic stainless steels in harsh chloride media. The corrosion conditions of the droplet evaporation test from which these data are derived are severe because the test temperature is high at 120°C (248°F) and the chloride solution is concentrated due to evaporation. In the test, the two duplex stainless steels 2205 and 2507 eventually broke when the stress reached a certain percentage of their yield strength, but this percentage was much higher than the corresponding percentage value of 316 stainless steel. Due to the ability of duplex stainless steel to resist stress corrosion cracking in the chloride aqueous solution under normal pressure, such as corrosion under the insulation layer, it is possible to consider the use of duplex stainless steel in the chloride medium where 304 and 316 stainless steels are known to fracture .
Table 4 summarizes the chloride stress corrosion fracture behavior of several stainless steels in various test media with different degrees of corrosion. The media on the left and right sides of the table are harsh because they contain acidic salts and high temperatures. The media conditions in the middle of the table are not so harsh. Standard austenitic stainless steels with a molybdenum content of less than 4% undergo chloride stress corrosion cracking under all these conditions, while duplex stainless steels are able to withstand the intermediate test conditions in the above intermediate range.
Hydrogen-resistant stress corrosion is affected by many factors, not only related to the ferrite content, but also to strength, temperature, hydrogen charging conditions, and applied stress. Although duplex stainless steel is sensitive to hydrogen-induced fracture, as long as the operating conditions are carefully evaluated and controlled, its strength advantages can still be utilized in hydrogen-containing media. The most prominent of these applications are high-strength pipelines that transport a mixture of brine and high-sulfur petroleum gas. Figure 10 illustrates the range of 2205 duplex stainless steels that are immune and sensitive to corrosion in acidic media containing sodium chloride.
The application of duplex stainless steel is becoming more and more extensive, and users are more and more familiar with this type of stainless steel. This article focuses on one of the difficulties of duplex stainless steel application-processing and welding, introduces the various characteristics of duplex stainless steel, and gives the basic principles and practical information for processing and welding duplex stainless steel.
Contents include: history, chemical composition, metallurgy, corrosion resistance, mechanical properties, physical properties, technical conditions, quality control, cutting, forming, welding, and applications of duplex stainless steel.
The full text is longer and will be published in several parts. Welcome to pay attention!
(Continued from the previous article)
5 Corrosion resistance
In the environment of most standard austenitic stainless steel applications, duplex stainless steels show high corrosion resistance, it is worth noting that they have very obvious advantages in some cases. This is due to their high chromium content, which is very beneficial in oxidizing acids, and contains sufficient amounts of molybdenum and nickel, which can resist the corrosion of medium reducing acid medium.
The relatively high chromium, molybdenum, and nitrogen contents of duplex stainless steels also make them resistant to chloride pitting and crevice corrosion. Their duplex structure is an advantage in environments where chloride stress corrosion cracking may occur.
If the microstructure of duplex stainless steel contains at least 25% to 30% ferrite, its resistance to chloride stress corrosion cracking is far better than that of austenitic stainless steel 304 or 316. However, ferrite is prone to hydrogen embrittlement, so duplex stainless steel has low corrosion resistance in environments or applications where hydrogen may enter the metal, and hydrogen embrittlement will occur.
5.1 Acid corrosion resistance
In order to illustrate the corrosion resistance of duplex stainless steel in strong acid solution, Figure 6 shows the corrosion data of sulfuric acid solution. The media conditions range from a weakly reducing environment with a low acid concentration to a high concentration oxidizing environment and a strong reducing environment with a medium concentration hot solution.
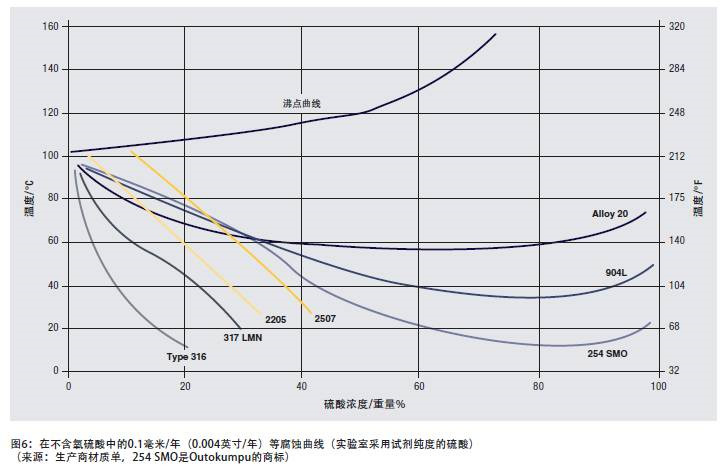
2205 and 2507 duplex stainless steels perform better than many high-nickel austenitic stainless steels in solutions with an acid concentration of up to about 15%; in the range of acid concentrations of at least 40%, duplex stainless steels are superior to 316 or 317 stainless steels.
Duplex stainless steel is also useful in this chloride-containing oxidizing acid.
The nickel content of duplex stainless steel is not enough to withstand the strong reducing corrosion of medium concentration sulfuric acid solution or hydrochloric acid. In a reducing environment, where there is a wet/dry interface where the acid is concentrated, corrosion, especially ferrite corrosion, will begin and progress rapidly.
The resistance to oxidation corrosion of duplex stainless steels makes them excellent candidates for nitric acid and strong organic acid installations.
Figure 7 shows the corrosion of duplex stainless steel and austenitic stainless steel in a mixed solution of 50% acetic acid and formic acid with different contents at the boiling temperature. Although 304 and 316 stainless steels can be used in strong organic acid media at room temperature and medium temperature, 2205 and other duplex stainless steels have advantages in many processes involving high-temperature organic acids, and because they are resistant to pitting and stress corrosion, they are also available Used in halogenated hydrocarbon process.
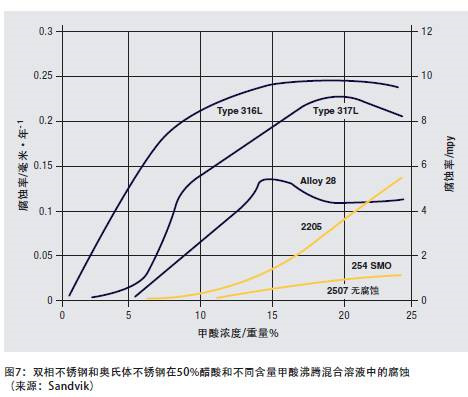
5.2 Alkali corrosion resistance
The high chromium content of the duplex stainless steel and the presence of the ferrite phase make it have good performance in alkaline media. At moderate temperatures, the corrosion rate is lower than that of standard austenitic stainless steels.
5.3 Resistance to pitting corrosion and crevice corrosion
In order to discuss the stainless steel's resistance to pitting and crevice corrosion, the concept of critical pitting temperature is introduced. For a certain chloride environment, each stainless steel can be characterized by a temperature. Above this temperature, pitting begins to occur, and it can develop to the extent visible to the naked eye within 24 hours. Below this temperature, pitting corrosion will not occur for an infinite period of time. This temperature is called the critical pitting temperature (CPT). It is a characterization of specific stainless steel grades and specific environments. Since the initial occurrence of pitting is statistically random, and CPT is sensitive to small changes in brands and products, CPT for different brands is usually expressed in a temperature range. The research tool introduced by the ASTM G 150 standard, namely the electrochemical measurement method, may be able to accurately and reliably determine CPT.
Crevice corrosion also has a similar critical temperature, called the critical crevice corrosion temperature (CCT). CCT depends on the characteristics of the stainless steel specimen, chloride environment and gap (tightness, length, etc.). Due to the geometry of the gap and the fact that it is difficult to reproduce the size of the same gap, the measurement data of CCT is more dispersed than CPT. Generally, for the same steel and in the same corrosive environment, CCT is often 15-20°C (27-36°F) lower than CPT.
The high chromium, molybdenum, and nitrogen of duplex stainless steels make them very resistant to chloride local corrosion in aqueous environments. Depending on the alloy content, some duplex stainless steel grades even rank among the best performing stainless steels. Duplex stainless steel has a relatively high chromium content, so it has good corrosion resistance and is very economical.
Figure 8 shows a comparison of the pitting and crevice corrosion resistance of some solution annealed stainless steels measured in accordance with ASTM G 48 2 (6% FeCl3). The critical temperature of the welding state of the material is lower. A high critical pitting or crevice corrosion temperature indicates that the material has a higher ability to resist the onset of corrosion. The CPT and CCT of 2205 steel are significantly higher than 316 stainless steel. This makes 2205 steel a versatile material suitable for environments where chloride ions are concentrated due to evaporation and under the steam space or insulation of heat exchangers. The CPT of 2205 duplex steel also shows that it can be used in alkaline water and degassed brine. It is also successfully used in degassed seawater. In these applications, the surface of the steel is free of deposits through high-velocity seawater or other methods.
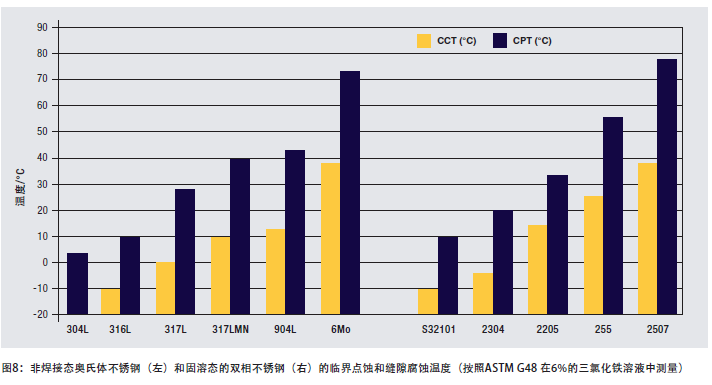
In demanding applications, such as thin-walled heat exchanger tubes, or deposits or cracks on the surface, 2205 duplex steel does not have sufficient resistance to crevice corrosion in seawater. However, high alloyed duplex stainless steels with a CCT higher than 2205, such as super duplex stainless steels, have been used in many harsh seawater conditions that require both high strength and resistance to chloride ion corrosion.
Because CPT is a function of materials and specific environments, it is possible to study the impact of a single element. Using the CPT determined according to the ASTM G 48 A method, the relationship between the composition of the steel (considering each element as an independent variable) and the measured CPT (correlated variable) is obtained by regression analysis. The results show that only chromium, molybdenum, tungsten and nitrogen have a stable effect on CPT. The relationship is as follows:
CPT = constant + %Cr + 3.3 (%Mo + 0.5%W) + 16%N.
The sum of the four alloy elements in the formula multiplied by their respective regression constants is usually called the equivalent pitting corrosion resistance (PREN). Different researchers give different coefficients of nitrogen, usually 16, 22 and 30. You can sort the brands of a family based on the PRE value, but you should pay attention to avoid excessive dependence on this relationship. The alloying elements in the formula are "independent variables", but they are not really independent, because the steel tested is a balanced composition. This relationship is not linear or cross-linked, for example, the synergistic effect of chromium and molybdenum is ignored. This relationship is only for materials in an ideal state, without considering the effects of intermetallic phases, non-metallic phases, and improper heat treatment. Improper heat treatment also adversely affects corrosion resistance.
5.4 Resistance to stress corrosion cracking
Some of the earliest applications of duplex stainless steels were based on their resistance to chloride stress corrosion cracking (SCC). Compared with austenitic stainless steels that have similar resistance to chloride pitting and crevice corrosion, duplex stainless steels exhibit significantly superior stress corrosion cracking resistance. Many applications of duplex stainless steels in the chemical processing industry replace the use of austenitic stainless steels where there is a high risk of stress corrosion cracking. However, like all other materials, duplex stainless steels are prone to stress corrosion cracking under certain conditions. This situation may occur at high temperatures, in chloride-containing environments, or in the presence of medium conditions that promote hydrogen-induced fractures.
Environmental conditions such as stress corrosion cracking may occur in duplex stainless steels, such as the 42% boiling magnesium chloride solution test, and the droplet evaporation test of the metal at high temperature and exposure to a pressurized aqueous chloride system (the temperature in the system may be higher than that under normal pressure) temperature).
Figure 9 shows the relative chloride stress corrosion cracking resistance of several rolled annealed duplex stainless steels and austenitic stainless steels in harsh chloride media. The corrosion conditions of the droplet evaporation test from which these data are derived are severe because the test temperature is high at 120°C (248°F) and the chloride solution is concentrated due to evaporation. In the test, the two duplex stainless steels 2205 and 2507 eventually broke when the stress reached a certain percentage of their yield strength, but this percentage was much higher than the corresponding percentage value of 316 stainless steel. Due to the ability of duplex stainless steel to resist stress corrosion cracking in the chloride aqueous solution under normal pressure, such as corrosion under the insulation layer, it is possible to consider the use of duplex stainless steel in the chloride medium where 304 and 316 stainless steels are known to fracture .
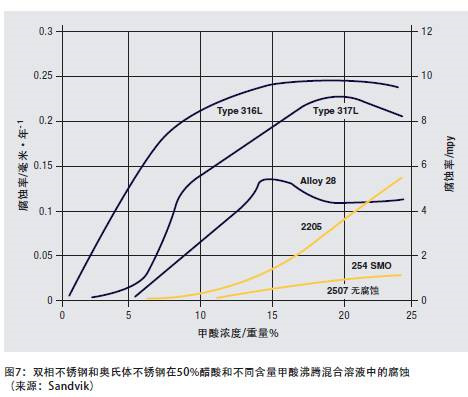
Table 4 summarizes the chloride stress corrosion fracture behavior of several stainless steels in various test media with different degrees of corrosion. The media on the left and right sides of the table are harsh because they contain acidic salts and high temperatures. The media conditions in the middle of the table are not so harsh. Standard austenitic stainless steels with a molybdenum content of less than 4% undergo chloride stress corrosion cracking under all these conditions, while duplex stainless steels are able to withstand the intermediate test conditions in the above intermediate range.
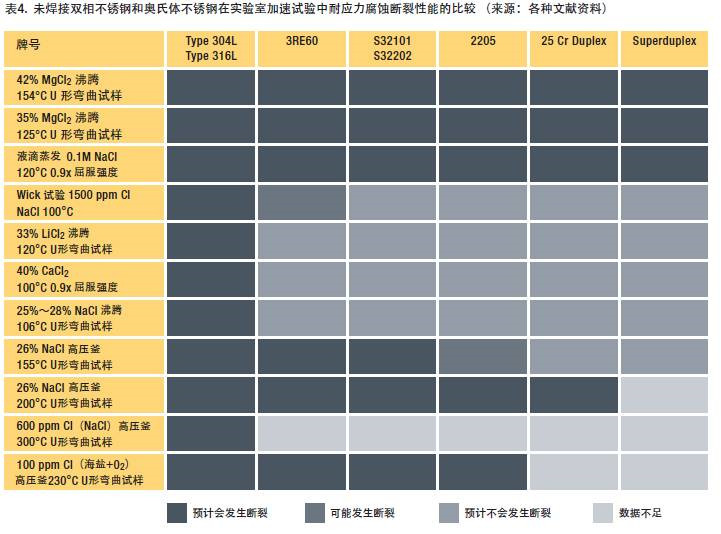
Hydrogen-resistant stress corrosion is affected by many factors, not only related to the ferrite content, but also to strength, temperature, hydrogen charging conditions, and applied stress. Although duplex stainless steel is sensitive to hydrogen-induced fracture, as long as the operating conditions are carefully evaluated and controlled, its strength advantages can still be utilized in hydrogen-containing media. The most prominent of these applications are high-strength pipelines that transport a mixture of brine and high-sulfur petroleum gas. Figure 10 illustrates the range of 2205 duplex stainless steels that are immune and sensitive to corrosion in acidic media containing sodium chloride.
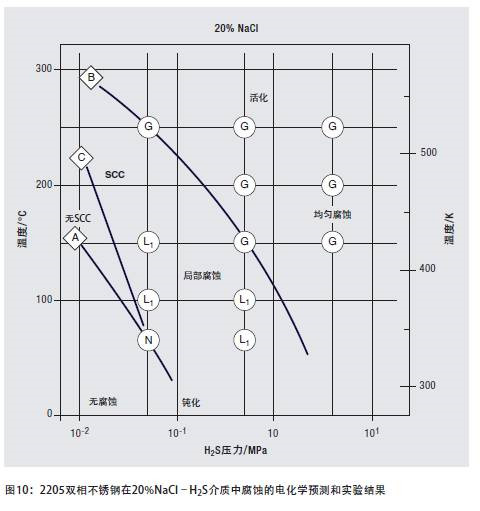
(To be continued)