Duplex Stainless Steel Processing and Manufacturing (1)
Practical Guide for Duplex Stainless Steel Processing and Manufacturing (1)
The application of duplex stainless steel is becoming more and more extensive, and users are more and more familiar with this type of stainless steel. This article focuses on one of the difficulties of duplex stainless steel application-processing and welding, introduces the various characteristics of duplex stainless steel, and gives the basic principles and practical information for processing and welding duplex stainless steel.
Contents include: history, chemical composition, metallurgy, corrosion resistance, mechanical properties, physical properties, technical conditions, quality control, cutting, forming, welding, and applications of duplex stainless steel.
The full text is longer and will be published in several parts. Welcome to pay attention!
1 Introduction
Duplex stainless steel is a type of steel that combines excellent corrosion resistance, high strength, and ease of manufacturing and processing. Their physical properties are between austenitic stainless steel and ferritic stainless steel, but they are closer to ferritic stainless steel and carbon steel. Duplex stainless steel's resistance to chloride pitting and crevice corrosion is related to its chromium, molybdenum, tungsten and nitrogen content. It can be similar to 316 stainless steel or higher than seawater stainless steel such as 6% Mo austenitic stainless steel. All duplex stainless steels are significantly more resistant to chloride stress corrosion cracking than 300 series austenitic stainless steels, and their strength is much higher than that of austenitic stainless steels. They also exhibit good plasticity and toughness.
The manufacturing process of duplex stainless steel has many similarities with the manufacturing process of austenitic stainless steel, but there are also important differences. The high alloy content and high strength of duplex stainless steel require some changes in the manufacturing process. This article is for processing manufacturers and end users who undertake manufacturing tasks. It provides practical information about the processing and manufacturing of duplex stainless steel. This article assumes that the reader already has experience in processing and manufacturing stainless steel. Therefore, the comparative data between the performance and processing technology of duplex stainless steel and 300 series austenitic stainless steel and carbon steel are given.
The processing and manufacturing of duplex stainless steel is different from ordinary stainless steel, but it is not difficult.
2 History of duplex stainless steel
Duplex stainless steel has a history of nearly 80 years, it is a mixed microstructure, austenite phase and ferrite phase each account for about half.
The early grades were alloys of chromium, nickel and molybdenum. The first batch of forged duplex stainless steel was produced in Sweden in 1930 and used in the sulfite paper industry. These grades were developed to reduce the intergranular corrosion problems of early high-carbon austenitic stainless steels. In 1930, Finland produced duplex stainless steel castings. In 1936, the predecessor of Uranus 50 was patented in France. After World War II, AISI 329 stainless steel became a recognized steel grade and was widely used in the heat exchanger pipes of nitric acid plants. 3RE60 is one of the first generation of duplex stainless steel grades specially developed to improve chloride stress corrosion cracking (SCC) resistance; later, forged and cast duplex stainless steel grades are used in various processing industry applications, including containers , Heat exchangers and pumps.
The first-generation duplex stainless steel has good performance, but it has limitations in the welded state. The heat-affected zone (HAZ) of the weld is low in toughness due to too much ferrite, and its corrosion resistance is significantly lower than that of the base material. These limitations limit the application of the first-generation duplex stainless steel to some specific applications in the non-welded state. The invention of the stainless steel refining process in 1968, that is, Argon Oxygen Decarburization (AOD), made it possible to produce a series of new stainless steel grades. One of the many advances brought by AOD is the deliberate addition of alloying element nitrogen. The addition of nitrogen in duplex stainless steel can make the toughness and corrosion resistance of HAZ in the welded state close to the performance of the base material. As the stability of austenite increases, nitrogen also reduces the rate of formation of harmful intermetallic phases.
Nitrogen-containing duplex stainless steel is called second-generation duplex stainless steel. This new commercialization progress began in the late 1970s, which coincided with the development and market of the Beihai offshore oil and gas field, which required excellent chloride ion corrosion resistance, good manufacturing processability, and high-strength stainless steel. 2205 has become the main brand of the second generation of duplex stainless steel and is widely used in offshore oil platform gas gathering pipelines and processing facilities. Due to the high strength of this steel, the wall thickness can be reduced and the weight of the platform can be reduced, making this stainless steel very attractive.
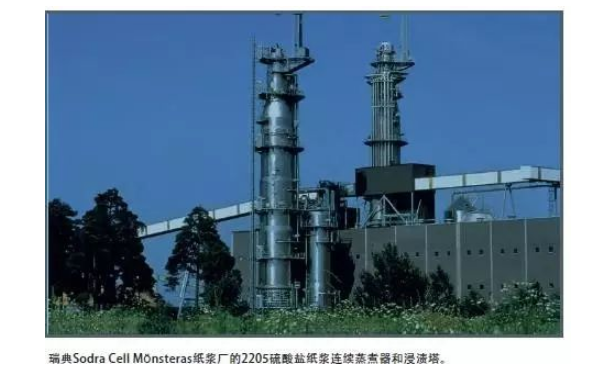
Like austenitic stainless steels, duplex stainless steels are a type of steel arranged according to corrosion characteristics, and the corrosion performance depends on their alloy composition. Duplex stainless steel has been constantly developing, and modern duplex stainless steel can be divided into 5 types:
① Economic duplex stainless steel without added molybdenum such as 2304;
②Standard duplex stainless steel such as 2205 is the main type of steel, accounting for more than 80% of the amount of duplex steel;
③25Cr duplex stainless steel such as alloy 255, PREN value is less than 40*;
④Super duplex stainless steel (PREN value 40~45), containing 25%~26%Cr, compared with the duplex stainless steel containing 25%Cr such as 2507, the content of molybdenum and nitrogen increases;
⑤ Special super duplex stainless steel, high alloyed duplex stainless steel with PREN value over 45
* PREN = equivalent number of pitting corrosion = %Cr+3.3(%Mo+0.5%W)+16%N
Table 1 shows the chemical composition of the second-generation forged duplex stainless steel and cast duplex stainless steel. For comparison, the first-generation duplex stainless steel and commonly used austenitic stainless steel are also included.
Table 1 Chemical composition of forged and cast duplex stainless steel* (% by weight)
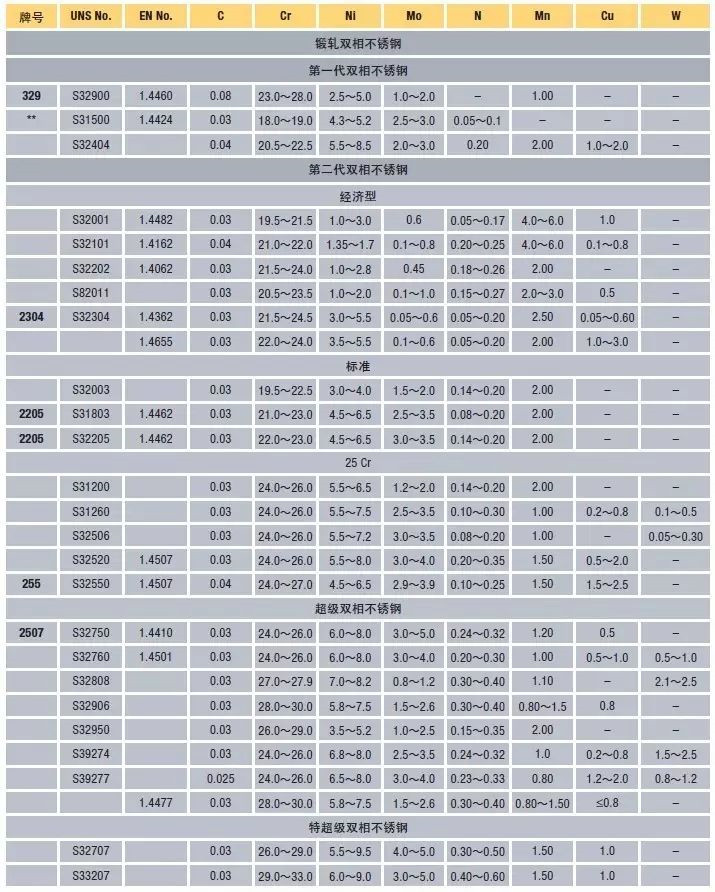
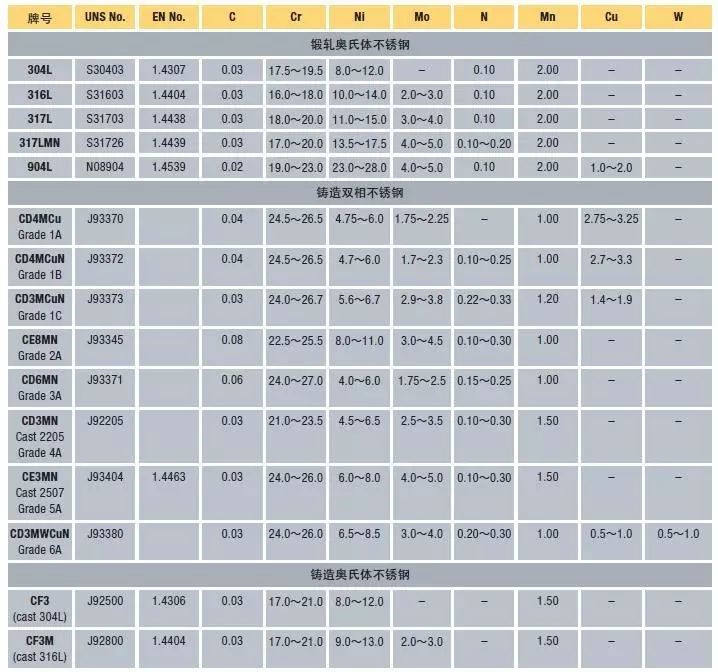
* Maximum value, unless the specified range or description is the minimum value.
-Not specified in the standard.
** This type of steel was originally not added with nitrogen and is considered to be the first generation of duplex stainless steel without nitrogen addition.
3 The role of chemical composition and alloying elements
3.1 Chemical composition of duplex stainless steel
It is generally believed that when the phase balance ratio of duplex stainless steel is 30% to 70%, ferrite is better than austenite, good performance can be obtained. However, duplex stainless steel is often considered to be roughly half of ferrite and austenite. In the current commercial production, in order to obtain the best toughness and processing characteristics, the proportion of austenite tends to be slightly larger. The interaction between the main alloying elements, especially chromium, molybdenum, nitrogen and nickel, is very complicated. In order to obtain a stable two-phase structure that is favorable for processing and manufacturing, care must be taken to make each element have an appropriate content.
In addition to phase equilibrium, the second major problem with duplex stainless steel and its chemical composition is the formation of harmful intermetallic phases at elevated temperatures. The σ phase and χ phase are formed in high-chromium and high-molybdenum stainless steel, and preferentially precipitate in the ferrite phase. The addition of nitrogen greatly delays the formation of these phases. Therefore, it is very important to maintain a sufficient amount of nitrogen in the solid solution. As the manufacturing experience of duplex stainless steels increases, the importance of controlling a narrow composition range becomes more and more obvious. 2205 dual-phase steel (UNS S31803, Table 1) initially set a wide range of compositions. Experience has shown that in order to obtain the best corrosion resistance and avoid the formation of intermetallic phases, the chromium, molybdenum and nitrogen content of S31803 should be maintained at The upper limit of the content range leads to the improved 2205 dual-phase steel UNS S32205 with a narrow composition range (Table 1). The composition of S32205 is the typical composition of 2205 duplex stainless steel commercialized today. In this article, unless otherwise stated, usually 2205 refers to S32205.
3.2 The role of alloying elements in duplex stainless steel
The following is a brief introduction to the influence of several most important alloying elements on the mechanical properties, physical properties and corrosion characteristics of duplex stainless steel.
chromium:
The chromium content in the steel must not be less than 10.5% to form a stable chromium-containing passivation film to protect the steel from atmospheric corrosion. The corrosion resistance of stainless steel increases with increasing chromium content. Chromium is a ferrite forming element, and the addition of chromium in steel can promote the formation of body-centered cubic ferrite. When the chromium content in the steel is high, more nickel needs to be added to form an austenite or dual-phase (ferrite-austenite) structure. Higher chromium content can also promote the formation of intermetallic phases. The chromium content of austenitic stainless steel is at least 16%, and the chromium content of duplex stainless steel is at least 20%. Chromium can also increase the oxidation resistance of steel at high temperatures. This role of chromium is very important, it affects the formation and removal of scale or tempered color after heat treatment or welding. Duplex stainless steel is more difficult to pick and remove tempering than austenitic stainless steel.
molybdenum:
The synergistic effect of molybdenum and chromium can improve the resistance of stainless steel to pitting corrosion. When the chromium content in stainless steel is at least 18%, the ability of molybdenum to resist pitting and crevice corrosion in chloride-containing environments is three times that of chromium. Molybdenum is a ferrite forming element and also increases the tendency of stainless steel to form intermetallic phases. Therefore, the molybdenum content of austenitic stainless steels is generally less than about 7.5%, and the molybdenum content of duplex stainless steels is less than 4%.
nitrogen:
Nitrogen improves the pitting and crevice corrosion resistance of austenitic and duplex stainless steels. It can also significantly increase the strength of steel. In fact, it is the most effective solid solution strengthening element and low-cost alloying element. The improvement of toughness of nitrogen-containing duplex stainless steel is attributed to its higher austenite content and the reduction of intermetallic phase content. Nitrogen does not prevent the precipitation of intermetallic phases, but it can delay the formation of intermetallic phases, allowing sufficient time for the processing and manufacturing of duplex stainless steels. Nitrogen is added to high corrosion resistance austenitic and duplex stainless steels with high chromium and molybdenum content to counteract their tendency to form sigma phases.
Nitrogen is a strong austenite forming element and can replace part of nickel in austenitic stainless steel. Nitrogen can reduce the stacking fault energy and improve the work hardening rate of austenite.
It also improves the strength of austenite through solid solution strengthening. Duplex stainless steels generally add nitrogen and adjust the nickel content in order to obtain an appropriate phase balance. The ferrite-forming elements chromium and molybdenum and the austenite-forming elements nickel and nitrogen are in balance to obtain a two-phase structure.
nickel:
Nickel is an element that stabilizes austenite, and nickel promotes the transformation of the crystal structure of stainless steel from a body-centered cubic structure (ferrite) to a face-centered cubic structure (austenite). Ferritic stainless steels contain very little or no nickel. Duplex stainless steels have low to medium nickel content, such as 1.5% to 7%. 300 series austenitic stainless steels contain at least 6% nickel (see Figures 1 and 2) ). The addition of nickel delays the formation of harmful intermetallic phases in austenitic stainless steels, but the delaying effect of nickel in duplex stainless steels is far less effective than nitrogen. The face-centered cubic structure makes the austenitic stainless steel have excellent toughness. Nearly half of duplex stainless steels are austenite, so the toughness of duplex stainless steels is significantly improved compared to ferritic stainless steels.
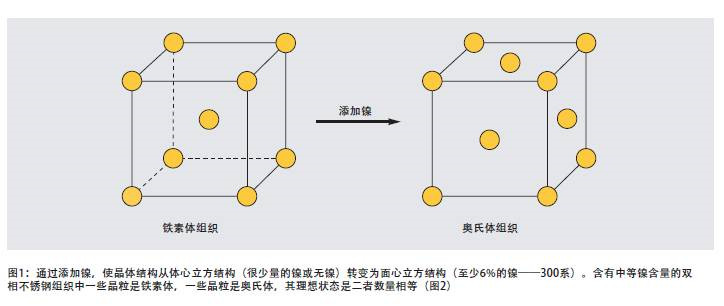
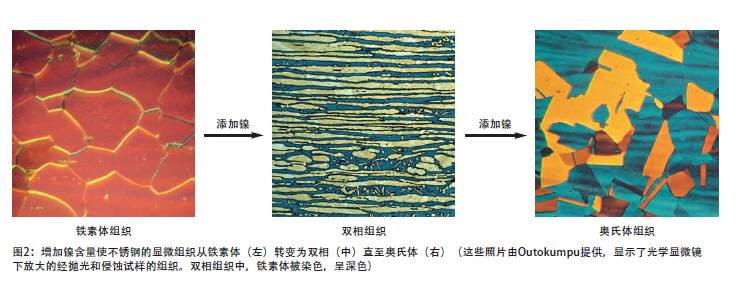
4 Metallurgy of duplex stainless steel
The ternary phase diagram of Fe-Cr-Ni alloy is a roadmap for the metallurgical behavior of duplex stainless steel. It can be seen from the ternary cross-sectional view (Figure 3) that the iron content is 68%: these alloys solidify with ferrite (a), and when the temperature drops to about 1000°C (1832°F), part of the ferrite transforms into Austenitic (g) (depending on alloy composition). At lower temperatures, the ferrite and austenite in equilibrium are hardly changed further. Figure 3 also shows the effect of increasing nitrogen. From a thermodynamic point of view, because austenite is transformed from ferrite, it is impossible for the alloy to skip the equilibrium state of austenite. However, when cooling continues to a lower temperature, carbides, nitrides, sigma phases, and other intermetallic phases may all become components of the microstructure.
The relative amounts of ferrite and austenite in metallurgical products or manufacturing processes depend on their chemical composition and heating history. As shown in the phase diagram, a small change in composition will have a greater impact on the relative volume fraction of the two phases. Separate ferrite forming elements and austenite forming elements also play a role in dual phase steel. The ferrite/austenite phase equilibrium in the microstructure can be predicted by the following multivariate linear regression:
Creq = %Cr + 1.73 %Si + 0.88 %Mo
Nieq = %Ni + 24.55 %C + 21.75 %N + 0.4 %Cu
% Ferrite = -20.93 + 4.01 Creq – 5.6 Nieq + 0.016 T
T (Celsius temperature) is the annealing temperature, 1050-1150°C, and the element content is weight percent (wt%).
In order to achieve the ideal phase balance of duplex stainless steel, mainly by adjusting the content of chromium, molybdenum, nickel and nitrogen, and control the heating operation. However, because the cooling rate determines the amount of ferrite that can be transformed into austenite, the cooling rate after high temperature heating will affect the phase balance. Because rapid cooling is beneficial for ferrite retention, it is possible to obtain more ferrite than in equilibrium. For example, the use of low heat input to weld large cross-section products will result in excessive ferrite in the HAZ (heat affected zone).
Another effective effect of nitrogen is to raise the temperature at which austenite begins to form from ferrite, see Figure 3, which increases the proportion of ferrite to austenite. Therefore, even under relatively rapid cooling conditions, the amount of austenite can almost reach the level of the equilibrium state. For the second-generation duplex stainless steel, this effect can reduce the problem of excessive HAZ ferrite.
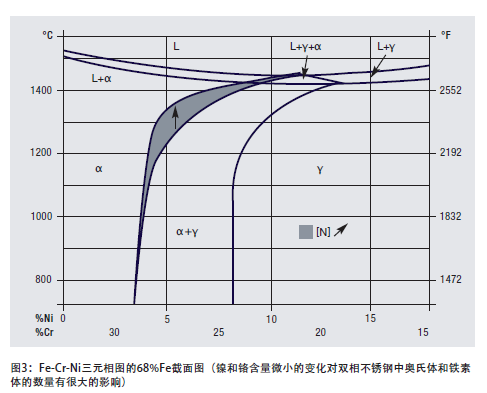
Because the formation temperature of σ phase is lower than the temperature at which ferrite transforms to austenite during cooling (Figure 4), in order to avoid σ phase in metallurgical products, the annealing temperature can be controlled to ensure that the steel is quenched from the annealing temperature as soon as possible to prevent the cooling process Σ phase is formed. The required cooling rate is very fast, and water quenching can be used. In actual manufacturing, the excessive cooling rate will only be encountered when the welding cross-sections differ greatly in size or when welding thick sections with very low heat input.
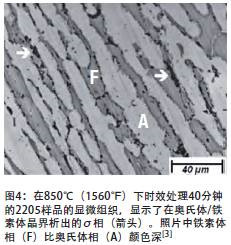
The α'phase in duplex stainless steel is also a stable phase. It is formed in the ferrite phase below 525°C (950°F), and its formation mechanism is the same as that of the α'phase in all-ferrite stainless steels. After ferrite stainless steel is exposed to a temperature of about 475°C (885°F) for a long time, the α'phase will cause the loss of normal temperature toughness, which is called 475°C/885°F brittleness.
In stainless steel, nitrogen as an alloy element means that chromium nitride may appear along the ferrite-ferrite grain boundary and austenite-ferrite phase boundary in the heat-affected zone of the weld. If its quantity is large, chromium nitride will adversely affect the corrosion resistance of the steel when the chromium-depleted zone is too late to compensate for the lost chromium. However, because higher nitrogen can promote the formation of austenite and austenite has a high solubility for nitrogen, the second-generation duplex stainless steel rarely contains a large amount of chromium nitride. In addition, the carbon content of the second-generation duplex stainless steel is very low, so it is usually not necessary to consider the harmful effects of carbides.
At certain temperatures, the harmful σ phase, α'phase, and carbide and nitride phases can be formed within a few minutes. Therefore, the processing and manufacturing and heat treatment during use must consider the reaction kinetics of phase formation to ensure that the required corrosion resistance and mechanical properties are obtained. These duplex stainless steel grades that have been developed now strive to have the best corrosion resistance and fully delay the precipitation reaction, so that the processing and manufacturing can proceed smoothly.
Figure 5 is an isothermal precipitation diagram of 2304, 2205 and 2507 duplex stainless steels. The precipitation time of chromium carbide and chromium nitride at the precipitation temperature is relatively "slow" 1 to 2 minutes. Duplex stainless steels precipitate more slowly than ferritic stainless steels or high-alloy austenitic stainless steels, partly due to the high solubility of carbon and nitrogen elements in the low-nickel austenitic phase and the delayed effect of nitrogen on carbide precipitation. Therefore, the duplex stainless steel grades have relatively strong resistance to sensitization during cooling. The formation kinetics of carbides and nitrides in these grades are only affected to a certain extent by chromium. The influence of molybdenum and nickel, therefore, the precipitation kinetics of all nitrogen-containing duplex stainless steel grades are similar to 2205 steel.
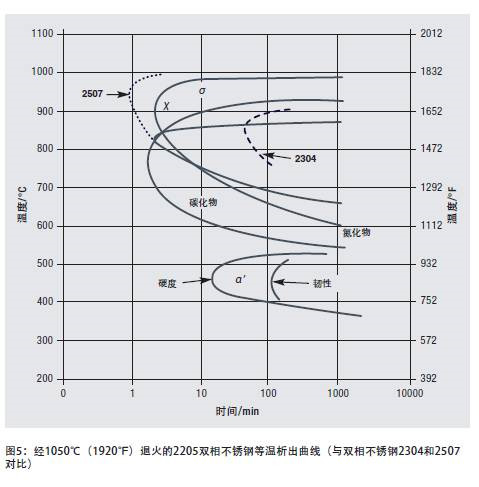
The precipitation temperature of σ phase and χ phase is slightly higher but it is about the same as the precipitation time of carbide and nitride. Duplex stainless steel grades with higher chromium, molybdenum and nickel content have faster σ phase and χ phase precipitation than 2205; low alloyed grades precipitate more slowly. The dotted line in FIG. 5 shows that the σ phase and the χ phase started to form earlier in the 2507 with higher alloying, and later in 2304.
The α'phase precipitates out of the ferrite phase, which hardens and embrittles the ferrite phase. Fortunately, duplex stainless steel contains 50% austenite, and the harm caused by this hardening and embrittlement is not as great as in all-ferrite stainless steel. The loss of toughness (brittleness) due to precipitation of the α'phase is slower than the rate of hardening (Figure 5). Because embrittlement takes a long time, the issue of α'phase brittleness is rarely considered in processing and manufacturing. However, the upper limit of the material's use temperature is restricted by the formation of α'phase.
Because long-term high-temperature use will cause the loss of steel's room temperature toughness, the pressure vessel design code has established the upper limit of the use temperature under the maximum allowable design stress. The German TüV code treats welded and non-welded structural parts differently, and its upper temperature limit is more conservative than ASME boiler and pressure vessel codes.
The temperature limits of various duplex stainless steels specified in the pressure vessel design specifications are shown in Table 2.
Table 3 summarizes some important precipitation reactions and temperature limits of duplex stainless steel.
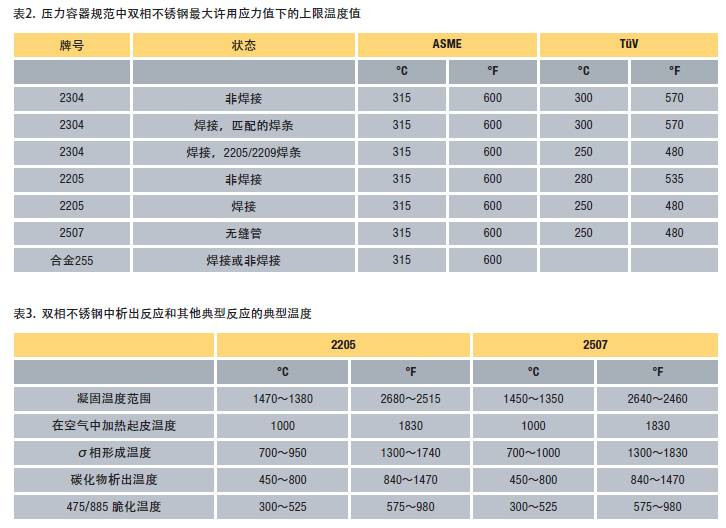