Duplex Stainless Steel Processing and Manufacturing (6)
Practical Guide for Processing and Manufacturing Duplex Stainless Steel (6)
The application of duplex stainless steel is increasing, and users are becoming more and more familiar with this type of stainless steel. This article focuses on one of the difficulties in the application of duplex stainless steel-machining and welding, introduces the various characteristics of duplex stainless steel, and gives the basic principles and practical information for processing and welding duplex stainless steel. The content includes: the history, chemical composition, metallurgy, corrosion resistance, mechanical properties, physical properties, technical conditions, quality control, cutting, forming, welding, application of duplex stainless steel.
The full text is longer and will be published in several parts, welcome to follow!
(Continued from the previous article)
13 Other connection methods
In addition to welding (melting the base material to connect), the advantages of other connection methods include minimal warpage and low residual stress. The joint can be leak-free and has considerable strength. However, the performance of non-welded joints will never be the same as that of welded joints, that is, the corrosion resistance and strength of the weld metal are as good as or almost as good as the base metal. This is an important consideration for duplex stainless steels that have better strength and corrosion resistance than 300 series austenitic stainless steels.
13.1 Bevel preparation
For all joining operations, it is very important to thoroughly clean the stainless steel before joining operations. The surface should be free of oil, grease, dust or fingerprints. Solvents should be used to remove these surface contaminations. Oil or grease will prevent the flux from removing the oxide layer in soldering and brazing. Loose surface contamination reduces the effective connection area. Generally, a product with a slightly rough surface is better connected than a smooth surface. Sometimes the roughening treatment with fine abrasives can increase the wettability of the surface, which is essential for a good connection.
13.2 Adhesive
Various commercial adhesives can be used to connect metal surfaces. Duplex stainless steel can be joined with adhesive in the same way as any other metal. Adhesive manufacturers can help users choose an adhesive suitable for specific connection strength, use temperature and use environment.
13.3 Soldering
The difference between soldering and brazing is the melting temperature of the filler material. The soldering temperature is usually below 450°C. Under normal circumstances, the joint strength of soft brazing is not as high as that of brazing, and the use temperature is lower than that of brazing. Typical solder filler materials include tin-lead, tin-antimony, tin-silver, and tin-lead-bismuth alloys. The joints processed by these low melting point filler materials have different strength and corrosion resistance and different color combinations.
In order to obtain good soldering, the oxide layer on the surface of stainless steel must be removed with flux before soldering. The protective oxide layer of stainless steel, especially molybdenum-containing duplex stainless steel, is highly stable, and it is very difficult to properly melt. Acidic flux will contain chloride. If chloride-containing flux is used, it must be rinsed with water or treated with a neutralizer immediately after soldering. Failure to completely remove the flux may cause pitting corrosion, even before the equipment is put into use.
13.4 Brazing
The melting point of the brazing filler material is above 450°C. Filler metals for brazing include silver brazing alloys, nickel brazing alloys and copper brazing alloys. The melting point of silver brazing alloys is relatively low, ranging from 618 to 705°C, the brazing temperature of copper alloys is between 1100 and 1150°C, and the melting point of nickel brazing alloys is higher, up to 1175°C. The use temperature of nickel brazed joints is higher than that of copper and silver brazed joints.
Duplex stainless steel should avoid the temperature range of 705~980℃. Therefore, braze at 1040°C or more or 705°C or less. When the temperature exceeds 1040℃, the brazed joint is quenched from the brazing temperature.
The appropriate brazing material should be selected according to the required corrosion resistance, use temperature and joint strength. Although not as corrosion-resistant as duplex stainless steel 2205, nickel brazing materials contain up to 25% chromium, giving them a certain degree of corrosion resistance.
It is reported that nitrogen-containing stainless steel is not easy to braze. This will affect the second-generation duplex stainless steel with higher nitrogen content. There are not many data available on the brazing of duplex stainless steel, so the manufacturer should conduct experiments to find the ideal brazing parameters.
Like soldering, in order to weld a good brazed joint, the oxide layer must be removed before and during brazing. Again, this is done with flux, which must be removed after brazing. The cleaning process is similar to soldering and includes cleaning with hot water or neutralizing chemicals.
14 Clean up after processing
The cleaning of duplex stainless steel after processing is no different from the requirements of other stainless steels. Cleaning after processing is very important, just as important as controlling the interlayer temperature or using shielding gas during welding. Stainless steel that is not properly cleaned after processing can fail at a much lower temperature than the base material or in a much less corrosive environment. This means that unless the best surface of the material is maintained or restored after processing, the additional cost of using materials with better corrosion resistance will be wasted. Welding spatter, welding oxide color, marking pen marks, arc starting point and undercut can all become gaps in the aqueous environment. At the same time, they can also have a different potential from the surface of stainless steel, so electrochemical reactions may occur. It is very important to eliminate these defects that have a destructive effect on the protective passivation film. Figure 18 summarizes these defects that may occur during the welding process and should be removed before the stainless steel is put into use.
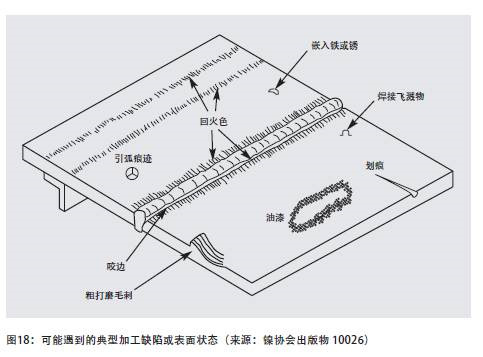
14.1 Marking pen marks, paint, dust and oil
All these surface contaminants can be the source of crevices and stainless steel pitting or crevice corrosion. In addition, they can also cause carbon pollution. If the next step of welding is carried out, carbide precipitation may occur. The material will undergo sensitization and intergranular corrosion during use. Use solvents to remove these contaminants.
14.2 Embedded iron (contamination by iron-containing compounds)
The embedded iron or free iron on stainless steel is caused by processing or transporting stainless steel with carbon steel tools. If you use carbon steel tools to process stainless steel, or process carbon steel near the place where the stainless steel is stored, the iron will transfer to the surface of the stainless steel. Subsequently, the iron rusts in a humid or humid environment and may cause corrosion of the stainless steel surface. The solution is to avoid all contact between stainless steel and carbon steel. Stainless steel processing should only use stainless steel tools, stainless steel wire brushes, stainless steel jigs and uncontaminated new grinding wheels. In the workshop, tools are often numbered in different colors.
It is often unrealistic and uneconomical to completely avoid the use of carbon steel tools and avoid iron pollution in the workshop environment. Therefore, iron contamination is acceptable but promises to ensure that the iron is removed before the stainless steel is put into use. Methods to remove iron contamination include mechanical cleaning, chemical cleaning or a combination of mechanical and chemical cleaning. The best cleaning method depends on the size and shape of the equipment, the expected usage, and certain practical issues including the disposal of cleaning waste. A common cleaning method is chemical treatment with nitric acid, which can dissolve free iron on the surface of stainless steel but does not corrode the protective layer of stainless steel or passive film. There are also many different chemical cleaning methods to achieve the desired results. ASTM A 380 (Cleaning, Descaling and Passivation of Stainless Steel Parts, Equipment and Systems) details cleaning methods. It is particularly important for users to be familiar with the safety issues described in ASTM A 380.
ASTM A 967 (chemical passivation treatment of stainless steel parts, instead of the US Federal Standard QQP-35c) describes how to choose an appropriate test method to prove that stainless steel has been effectively passivated. The standard expects users to define the required passivation level, allowing manufacturers to select cost-effective and appropriate methods for surface treatment.
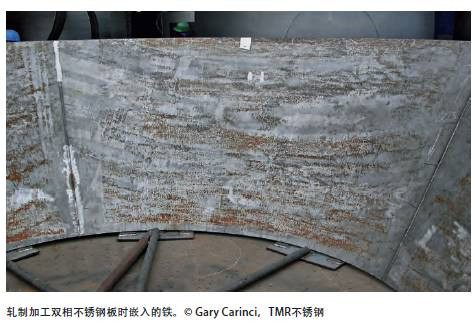
14.3 Welding spatter, welding discoloration, flux, welding slag, arc ignition spot
All these defects may occur during the welding process. They can form crevices and become a source of crevice corrosion in a chloride-containing environment. These defects should be avoided or removed after welding. The use of anti-spatter compounds during processing can prevent welding spatter. The discoloration of welding is due to the destruction of the passivation layer, so it will reduce the corrosion resistance. Protecting with inert gas and cleaning the back of the weld with inert gas can prevent serious welding discoloration or oxidation. However, oxidation color cannot be completely avoided and must be removed in post-weld cleaning. Before the equipment is put into use, the flux and slag inclusions and arc ignition spots should also be removed. Welding spatter, welding oxide color, flux, welding slag, arc ignition spot and welding undercut can all be removed by mechanical cleaning methods, such as fine grinding or the use of stainless steel wire wheels or brushes. The use of fine grinding wheels is very important, because the rough grinding marks will stick to deposits during use, forming gaps and causing corrosion.
A distinctive feature of duplex stainless steel is that the weld seam is thin and sticky, and it is more resistant to chemical cleaning than austenitic stainless steel with comparable corrosion resistance. The discoloration of the weld can be chemically cleaned by pickling, for example, 2205 is pickled with 20% nitric acid-5% hydrofluoric acid solution. The solution can dissolve chromium oxide, and can also attack stainless steel, thereby removing the chromium-depleted layer. Pickling paste has similar functions, but it is easier to handle large workpieces, so it can be used instead of acid solutions. However, it should be recognized that a harmful solution will be produced when cleaning with pickling cream, and the user is responsible for taking safe use and disposal measures. Depending on the corrosion resistance of duplex stainless steel, a weaker or stronger acid may be required to remove the oxidation color.
Studies have shown that chemical passivation after mechanical cleaning can obtain the best post-weld corrosion resistance.
(To be continued)