Analysis of corrosion resistance of stainless steel
Analysis of corrosion resistance of stainless steel
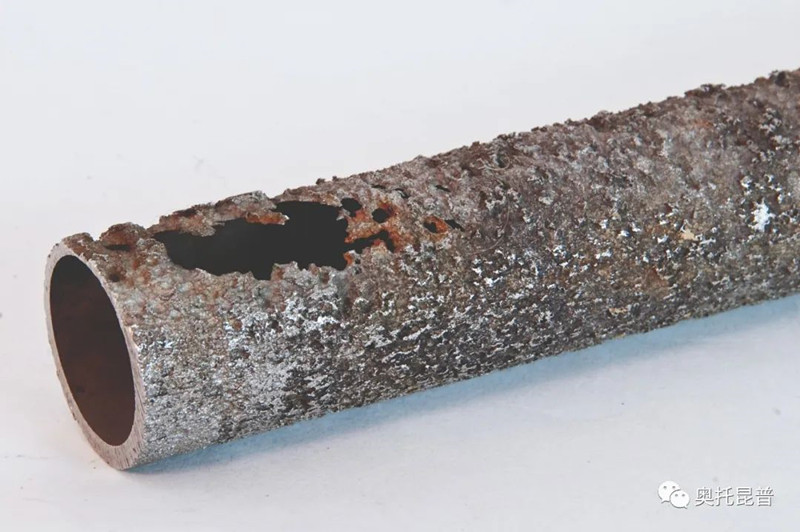
What is corrosion?
Corrosion is an electrochemical process in which metals react with the surrounding environment, and the resulting degradation triggers the loss of material properties (such as mechanical strength, appearance, and impermeability to liquids and gases). The cause of corrosion is the energy difference between the metal and its natural ore. Extracting any metal from ore requires energy. This "excess energy" promotes corrosion because the metal will try to return to its natural state.
Electrochemically speaking, corrosion is the release of electrons. The process of releasing electrons is called oxidation reaction or anode reaction. However, these electrons need to be consumed somewhere, so a reduction reaction or a cathode reaction needs to occur.
Metals that are easily oxidized (such as magnesium) are called non-precious (reactive) metals, while the most corrosion-resistant metals (such as gold and platinum) are called precious (inert) metals. Between the two, we found most metals for engineering purposes, such as iron and copper.
Passivation of stainless steel
In essence, stainless steel is not a precious metal like gold or platinum. The corrosion resistance of stainless steel comes from the invisible and insoluble thin layer composed of chromium and iron oxides and hydroxides, usually called the passivation film (Figure 1).
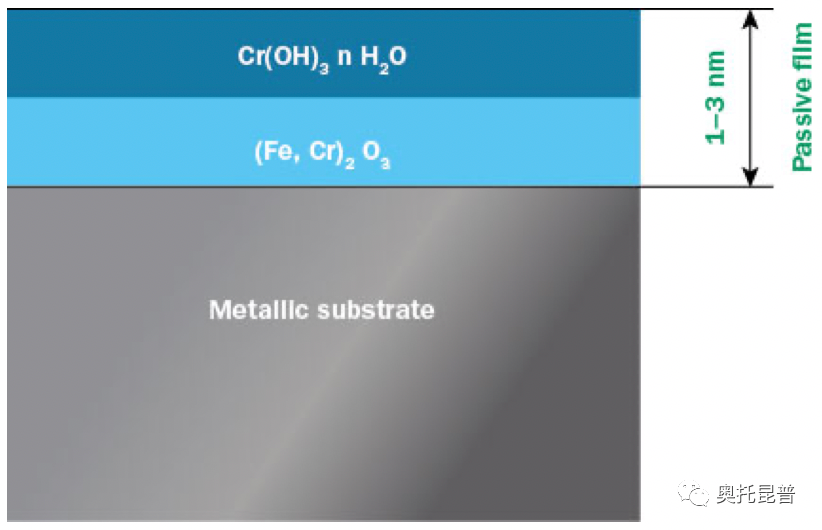
Figure 1: Two-layer model of stainless steel passive film
Even if the passivation film is only a few nanometers thick, it can effectively isolate the metal below from the surrounding environment, effectively slowing down the electrochemical reaction that causes corrosion, and the corrosion rate is much faster than the corrosion rate without the passivation film. reduce. Other metals (such as chromium, aluminum and titanium) also show passivation, and stainless steel is the ability to use chromium to passivate.
In an environment containing sufficient oxidant, the passive film on the surface of stainless steel will form spontaneously. In addition, if the metal under the passivation film is exposed due to mechanical damage (such as scratches), it will spontaneously re-passivate. The oxygen content in air and most aqueous solutions is sufficient to form and maintain a passive film on stainless steel. If the passivation film can be effectively retained, stainless steel can be used almost permanently.
Uniform corrosion
In an environment where the passivation film is unstable, uniform corrosion will occur, and the unprotected metal surface is more or less uniformly reduced, as shown in Figure 2. In acid or hot alkaline solutions, uniform corrosion of stainless steel is the most common. In addition, molten salts of chloride and fluoride can also cause uniform corrosion
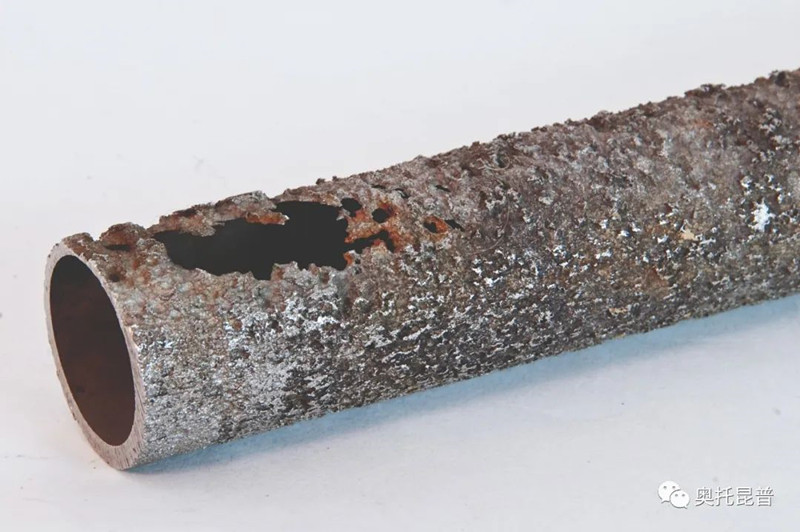
Figure 2: Uniform corrosion of steam pipes exposed to sulfuric acid
In an environment with constant temperature and chemical composition, it is expected that uniform corrosion will occur at a reasonable constant rate. By measuring the weight loss per unit time over a certain surface area, the corrosion rate can be determined. This is usually expressed as the loss of thickness over time, for example mm/year. By definition, if the corrosion rate does not exceed 0.1 mm/year, it is generally considered that stainless steel has the ability to resist uniform corrosion in a specific environment.
Pitting and crevice corrosion
Uniform corrosion can cause extensive damage to the passivation film, but pitting corrosion and crevice corrosion are caused by the local damage of the passivation film. In actual situations, the corrosion failure of stainless steel is usually the result of localized corrosion rather than uniform corrosion. Please refer to Figure 3. In this case, galvanic couples are formed locally on the surface of the stainless steel, which will cause rapid corrosion to spread. Compared with uniform corrosion, the weight loss of localized corrosion may be small, and the corrosion rate as an indicator of the severity of corrosion has nothing to do with localized corrosion. On the contrary, pitting corrosion and crevice corrosion are considered to be an either-or situation. Once local corrosion starts, it will penetrate the material very quickly, so it needs to be avoided.
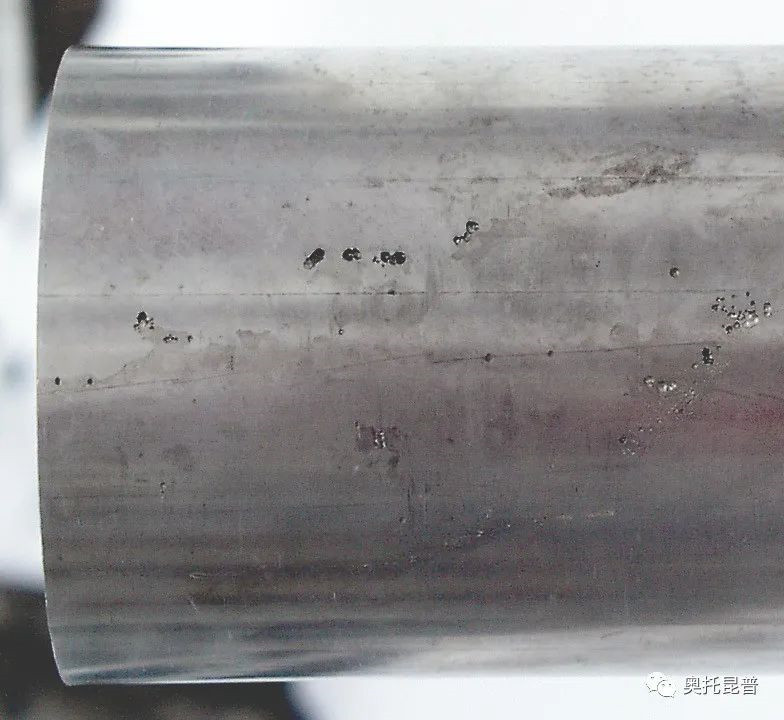
Figure 3: Pitting corrosion on the outside of the pipe
In environments containing halogen ions, such as chlorides, stainless steel is particularly prone to pitting and crevice corrosion. Therefore, environments where there is a risk of localized corrosion include liquids containing large amounts of chlorides, such as sea water and various industrial solutions.
Crevice corrosion (see Figure 4) occurs in crevices and other confined spaces, as well as under deposits formed during use. In an aqueous environment, the natural chemical reaction on the surface of stainless steel consumes oxygen. In the stagnant solution inside the gap, the supply of new oxidant is restricted. The composition of the solution in the gap gradually becomes different from the composition of the surrounding solution. When forming a concentration difference battery, this difference in composition increases the risk of corrosion.

Figure 4: Crevice corrosion under flange seals exposed to chlorinated seawater
An increasingly corrosive environment will eventually destroy the passivation film inside the crevice, and a small exposed metal surface will act as an anode for a larger passivation area around the crevice.
For any type of corrosion, the risk of pitting and crevice corrosion depends on environmental factors and the corrosion resistance of the alloy. High chloride concentration, low pH and high temperature all increase the possibility of pitting and crevice corrosion. Other halides (such as bromide and iodide) may also cause pitting and crevice corrosion.
Stress corrosion cracking
Stress corrosion cracking (SCC) is a brittle failure mode caused by the combined action of mechanical stress and corrosive environment. In an environment where pitting, crevices, or uniform corrosion is not expected, it may cause rapid loss of mechanical strength, and may lead to catastrophic failure of rupture, which makes it a hidden form of corrosion. The occurrence of stress corrosion cracking must meet three requirements:
• Susceptible materials
• Environments where materials are sensitive to stress corrosion cracking
• Sufficient tensile stress
If one of these three factors is removed, stress corrosion cracking will not occur. Like pitting and crevice corrosion, the most common causes of stress corrosion in stainless steel are chloride-containing solutions and high temperatures. As the chloride concentration increases, the temperature increases and the pH value decreases, the risk of stress corrosion cracking also increases. The stress corrosion of stainless steel usually appears in the form of small, branched cracks, as shown in Figure 5.
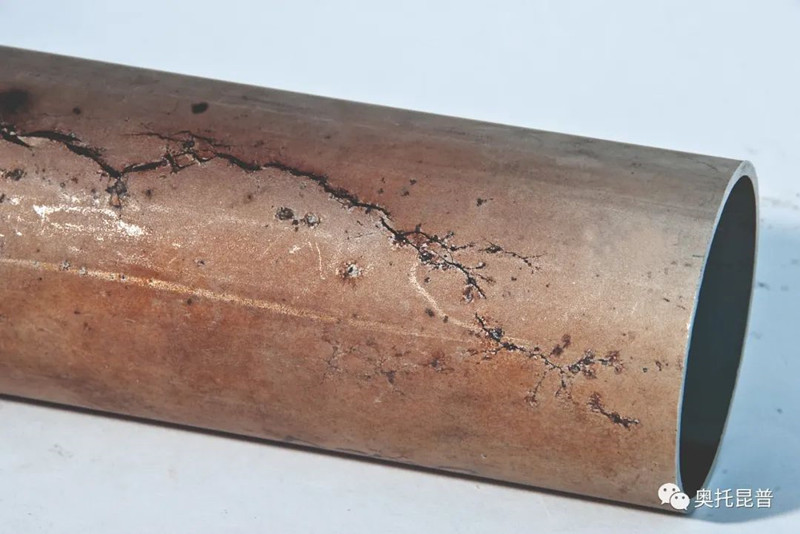
Figure 5: Stress corrosion cracking of stainless steel pipe
Due to the rapid growth of cracks, failures caused by stress corrosion cracking usually occur suddenly without warning. In the most severe cases, component failure may occur within days or even hours.
Corrosion fatigue
When a material is subjected to periodic loads, it can fail under a load far below the ultimate tensile stress of the material. If the material is exposed to a corrosive environment at the same time, even under a lower load, failure may occur in a short time. This is caused by a type of corrosion called corrosion fatigue, which is similar to stress corrosion cracking and causes brittle failure. However, there are fewer crack branches due to corrosion fatigue, as shown in Figure 6. Corrosion fatigue usually occurs in normal temperature environments and neutral solutions.
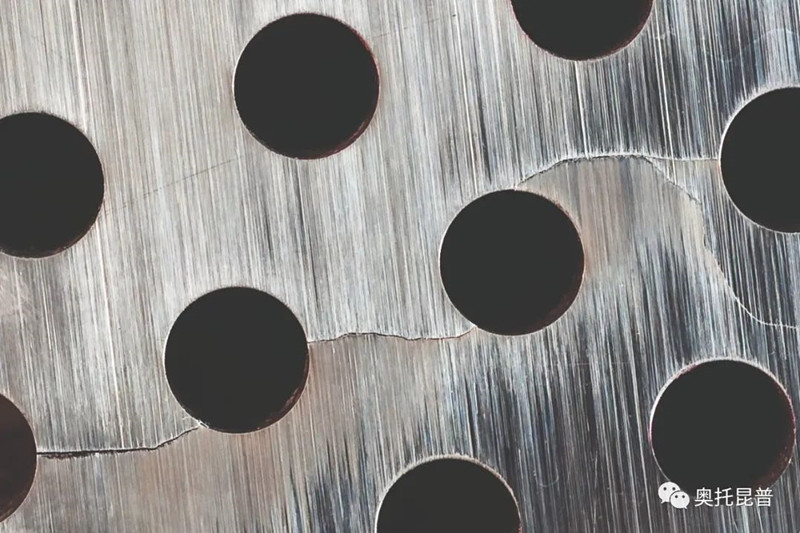
Figure 6: Corrosion fatigue cracks in the suction roll shell of a paper machine
Intergranular corrosion
Intergranular corrosion refers to a kind of local corrosion in which the grain boundaries and adjacent parts of the material are preferentially corroded, but the grain itself is not corroded or corroded very slightly, as shown in Figure 7. In stainless steel, the precipitation of chromium carbide or intermetallic phases may cause intergranular corrosion. Due to the high carbon content of previous stainless steels (0.05-0.15%), this corrosion is potentially dangerous. The use of AOD (Argon Oxygen Refining Furnace) in the production of modern stainless steel has reduced the carbon content, so intergranular corrosion has rarely become a problem today.

Figure 7: Intergranular corrosion of stainless steel tubes
Galvanic corrosion
Galvanic corrosion is the electrochemical corrosion of two different metals in contact with each other while being in the electrolyte. Generally, the more active metal (anode) will be more severely corroded, while the inert metal (cathode) will be protected. Usually this kind of galvanic corrosion is most likely to occur near the junction of two metals, see Figure 8.
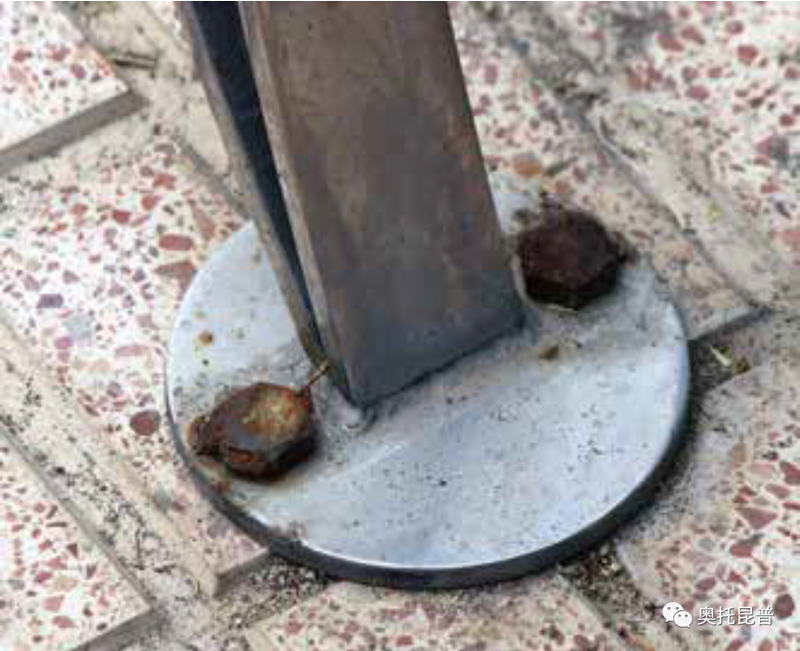
Figure 8: Galvanic corrosion of galvanized bolts connected to stainless steel
As long as stainless steel remains passivated, they will be more inert than other metal materials in most environments, so they are cathodes in most galvanic couples. On the other hand, resistance coupling with stainless steel may increase the corrosion rate of non-precious metals such as high carbon steel, galvanized steel, copper and brass. Galvanic corrosion between different stainless steel grades is usually not a problem, provided that each stainless steel is passivated in a specific environment.